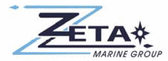
Catalog excerpts
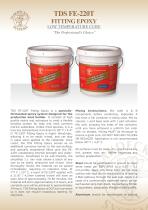
TDS FE-220T F ITT ING EPOXY LOW TEMPERATURE CURE “The Professional’s Choice ” TDS FE-220T Fitting Epoxy is a specially-formulated epoxy system designed for the production boat builder. It consists of high quality resins and activators to yield a flexible bonding system for teak and most common marine substrates. Unlike most epoxies, it is a true low temperature cure down to 40° F / 4,4° C! FE-220T Fitting Epoxy is highly thixotropic, allowing it to be easily mixed, and yet stay in place when applied to the substrate. Once cured, the TDS Fitting Epoxy serves as an additional corrosion barrier to the sub-surface, and specially engineered fillers give the FE-220T outstanding internal strength and water-resistance. Developed to be user-friendly, the simplified 1:1 mix ratio allows a batch of any size to be easily measured and mixed. Once thoroughly mixed, the material can be spread immediately, requiring no induction time. At 77° F / 25° C, a layer of FE-220T applied with a 3/16" / 4,5mm toothed trowel will have an open time of approximately 70-80 minutes, the material will set in approximately 4-6 hours, and complete cure will be achieved in approximately 24 hours. TDS Fitting Epoxy is DOT non-corrosive so it does not require hazardous labeling for shipment. Mixing Instructions: Stir both A & B components before combining, especially if less than a full container is being used. Mix by volume: 1 part base resin with 1 part activator. Mix well, scraping the sides of the container, until you have achieved a uniform tan color with no streaks. Mixing MUST be thorough to ensure a good cure. DO NOT ADD ANY FILLERS OR REDUCER. Application is not recommended below 40° F / 4,4° C. All surfaces must be clean, dry, and free of any dirt, grease, wax, etc. before beginning any surface preparation. Steel should be sandblasted or ground to clean white metal per SSPC-SP63 to a 0,07 - 0,1 mm profile. Wash with Metal Prep. Do not wipe surface with rags due to the possibility of leaving a fiber pathway through the seal coat. Apply 2-3 coats of a commercially approved epoxy primer such as Awl-Grip High-Build, Devoe Epoxy Primer or equivalent, adequately filling the blast profile. Aluminum should be sandblasted or ground
Open the catalog to page 1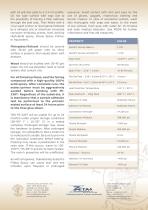
with 24 grit disc pads to a 3-4 mil profile. Do not wipe surface with rags due to the possibility of leaving a fiber pathway through the seal coat. Then follow with a vinyl wash primer or Alumaprep followed by a mil/spec zinc or strontium chromate corrosion-inhibiting primer, then AwlGrip High-Build epoxy, Devoe Epoxy Primer, or equivalent. Fiberglass/Gelcoat should be ground with 36-40 grit paper until no shiny surface is present, then wiped down with acetone. Wood should be scuffed with 36-40 grit paper. Do not use polyester resin or wood sealers that contain oils. For all faired...
Open the catalog to page 2All Zeta Marine Group ApS. catalogs and brochures
-
FE180A
2 Pages
-
y SIS440
1 Pages
-
TDS Adhesion Promoter
1 Pages
-
TDS Sealer & Protector
1 Pages
-
TDS PROFESSIONAL TOOLS
1 Pages
-
ECO-300
2 Pages
-
ECO-100
2 Pages
-
FE 180A EPOXY DATA SHEET
2 Pages
-
TDS FR-101
2 Pages
-
TDS AP-100
2 Pages
-
TDS FE-180
2 Pages
-
TDS FFE-200
2 Pages