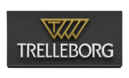
Group: Trelleborg

Catalog excerpts
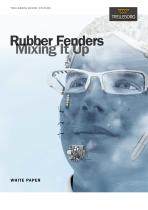
Rubber Fenders Mixing It Up
Open the catalog to page 1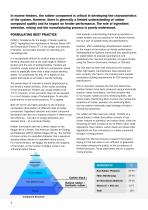
In marine fenders, the rubber component is critical in developing the characteristics of the system. However, there is generally a limited understanding of rubber compound quality and its impact on fender performance. The role of ingredient selection, mixing and the manufacturing process is poorly understood. FORMULATING BEST PRACTICE PIANC’s “Guidelines for the design of fender systems, 2002” highlighted the importance of Velocity Factor (VF) and Temperature Factor (TF) in the design and selection of fenders, and provides direction for reporting and calculating both. It is exceptionally...
Open the catalog to page 2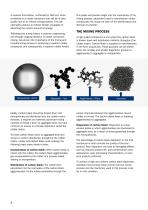
A superior formulation, confirmed by TGA test, when converted to a rubber compound can still be of poor quality due to an inferior mixing process. This can ultimately produce an inferior fender, incapable of absorbing the correct amount of energy. Trelleborg has a long history in polymer engineering, and through ongoing research in rubber compound mixing, has proven the importance of the mixing and manufacturing process in producing a superior rubber compound, and subsequently, a superior rubber fender. Ideally, carbon black should be broken down into nanoparticles and distributed into the...
Open the catalog to page 3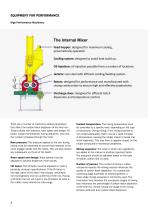
High Performance Machinery Feed hopper: designed for maximum cooling, pneumatically operated. Cooling system: designed to avoid heat build up. Oil injection: oil injection possible from a number of locations. Jackets: cast steel with efficient cooling/heating system. Rotors: designed for performance and manufactured with strong construction to ensure high and effective productivity. Discharge door: designed for efficient batch dispersion and temperature control. There are a number of machinery related parameters that affect the carbon black dispersion of the final mix. These include ram...
Open the catalog to page 4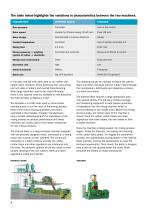
The table below highlights the variations in characteristics between the two machines. PARAMETERS INTERNAL MIXER Lack of fine control Rotor speed Variable for efficient mixing (20-60 rpm) Rotor design Sophisticated to improve dispersion Coolant temperature Lack of precise controlled unit Mixing time Mixing sequence + weighing system of rubber + chemicals Manual and difficult to control Mixing room environment Operation cost Initial investment Batch size In the past, two roll mills were used to mix rubber with carbon black. However, this is extremely time consuming and not viable in today’s...
Open the catalog to page 5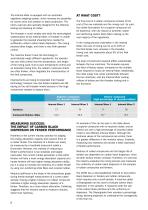
The Internal Mixer is equipped with an automatic ingredient weighing system, which removes the possibility for human error and variation in batch production. The rotors used are also specially designed for the effective tearing and shearing of rubber. The Kneader is much smaller and lacks the technological sophistication of the Internal Mixer. A Kneader is unable to generate the required shearing force needed for sufficiently uniform carbon black dispersion. The mixing process takes longer, and there is very little operator control. The machine doesn’t have the technology to automatically...
Open the catalog to page 6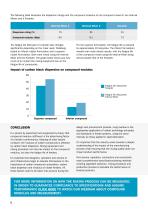
The following table illustrates the dispersion ratings and the compound modulus of one compound mixed in two Internal Mixers and a Kneader. Internal Mixer 1 Dispersion rating (%) The fatigue life (lifecycle) of a fender also changes significantly depending on the mixer used. Trelleborg tested an inferior rubber formulation and a superior rubber formulation. Both were mixed using the Internal Mixer and the Kneader. The graph below shows just how much of an impact the mixing equipment has on the fatigue life of compounds. For the superior formulation, the fatigue life is reduced by...
Open the catalog to page 7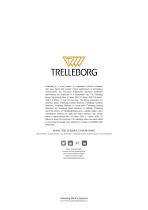
Trelleborg is a world leader in engineered polymer solutions that seal, damp and protect critical applications in demanding environments. Its innovative engineered solutions accelerate performance for customers in a sustainable way. The Trelleborg Group has annual sales of about SEK 21 billion (EUR 2.3 billion, USD 3.2 billion) in over 40 countries. The Group comprises five business areas: Trelleborg Coated Systems, Trelleborg Industrial Solutions, Trelleborg Offshore & Construction, Trelleborg Sealing Solutions and Trelleborg Wheel Systems. In addition, Trelleborg owns 50 percent of...
Open the catalog to page 8All Trelleborg Marine and Infrastructure catalogs and brochures
-
SafePilot brochure
20 Pages
-
Docking & Mooring
88 Pages
-
Pneumatic Fender infographic
1 Pages
-
Pneumatic Fenders brochure
28 Pages
-
Fender Application Design Manual
88 Pages
-
Multipurpose and Tug Fenders
44 Pages
-
Rolling Fenders and Safety
18 Pages
-
AutoMoor Brochure
24 Pages
-
Fender Systems
86 Pages
-
DynaMoor
20 Pages
-
Bollards
28 Pages
-
Solid SmartFender Factsheet
2 Pages
-
Ship-Shore Links Factsheet
4 Pages
-
SmartDAS Factsheet
2 Pages
-
TRELLEBORG DYNAMOOR
4 Pages
-
SmartDock ® Display Board
4 Pages
-
Surface Buoyancy
24 Pages
-
SmartMoor Series II
7 Pages
-
Performance Monitoring
3 Pages
-
Universal Safety Link
3 Pages
-
TRELLEBORG’S Tugger Winch
2 Pages
-
LNG Infographic
8 Pages
-
SafePilot User Guide
30 Pages
-
Safepilot SmartPort System
16 Pages
-
Combined ESDS & SSL
3 Pages
-
Ship Shore Link System
3 Pages
-
Emergency Shutdown Link
3 Pages
-
Floating Fenders
48 Pages
-
Prelude LNG
1 Pages
-
AutoMoor Datasheet
4 Pages
-
SafePilot CAT XT System
2 Pages
-
Whitepaper - Correction Factors
10 Pages
-
Mini Guide - Foam Fenders
5 Pages
-
Buoy Range Table
2 Pages
-
Hawser Hooks
6 Pages
-
Guide - Fenders
8 Pages
-
Barometer Report 3
16 Pages
-
Barometer Report 2
7 Pages
-
lload monitoring software
2 Pages
-
lload monitoring systeme
5 Pages
-
Remote Release System
6 Pages
-
Capstans
4 Pages
-
Accessories
10 Pages
Archived catalogs
-
Docking and mooring
2 Pages