

Catalog excerpts
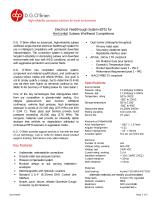
Electrical Feedthrough System (EFS) for Horizontal Subsea Wellhead Completions D.G. O Brien offers an advanced, high-reliability subsea wellhead single-channel electrical feedthrough system for use in intelligent completions with permanent downhole instrumentation. The connection system is designed for long-term reliability in demanding subsea and downhole environments with sour well (H2S) conditions, as well as with aggressive production and packer fluids. D.G. O Brien has completed extensive system, component and material qualifications, and continues to analyze failure modes and effects (FMEA). Our goal is not to simply qualify a design, but to determine its limits and set them ever higher as demands continue to rise. (Refer to the Summary of Testing below for more detail.) One of the key technologies that distinguishes DGO from our competition is glass-to-metal sealing. Our integral glass-ceramic seal barriers withstand continuous, extreme high pressure, high temperature exposure in excess of 22,500 psig (155 MPa) and 400 F (204 C). These glass seal barriers provide burst pressures exceeding 40,000 psig (276 MPa). The inorganic materials used provide an inherently stable structure that exhibits no degradation attributed to continuous HPHT exposure in aggressive media. D.G. O Brien provides support services in line with the level of our technology. Call or write for details about product support, training, field service and custom designs. Underwater, wetmateable connections Glass-to-metal seal pressure barriers Pressure compensated system Modular design to suit varying installation envelopes Interchangeable with hydraulic couplers Standard 1/4 (6.35mm) DHG Control Line interface Simple, quick, secure, reliable Downhole Gauge connector rig terminations Dual barrier philosophy throughout: − Primary metal seals − Secondary elastomer seals − Rig-testable interface seals API 6A, 16D & 17D compliant − HH Material class (sour service) − Exceeds U Temperature class − Product Specification Level 3 PSL 3 − Performance Requirement Level 2 PR2 NACE MR0175 compliant Specifications: Environmental Pressure, rating Pressure, test Temperature, rating Deployment depth Mating durability Service life Mechanical (maximums) Axial misalignment Angular misalignment Radial misalignment Actuation speed Electrical Number of circuits Voltage rating, working Voltage, test Current rating, working Insulation resistance Contact resistance Shell resistance Materials Load bearing Storage temperature alternate materials are readily accommodated Metal seals Dielectric insulators Elastomers Electrical contacts Inconel 718, Ag-plated PEEK FKM and HNBR Au-plated BeCu Page 1 of 5
Open the catalog to page 1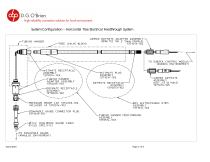
WM High-reliability connection solutions for harsh environments JUMPER DRYMATE ADAPTER ASSEMBLY- TO SUBSEA CONTROL MODULE (SUBSEA ENVIRONMENT) ■JUMPER DRYMATE TUBING HANGER FEEDTHROUGH >1/4" DOWNHOLE GAUGE CABLE (FIELD SPECIFIC) (ANNULUS ENVIROMENT)
Open the catalog to page 2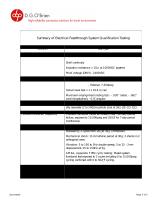
Summary of Electrical Feedthrough System Qualification Testing Function Electrical Test Type Contact resistance < 30mΩ at 2A (per contact pair) Shell continuity Insulation resistance > 1GΩ at 1000VDC (system) Proof voltage (DWV) - 2400VDC Pressure testing Helium leak test < 1 x 10-6 cc/sec Maximum misalignment mating test - –.030 radial, –.062 axial (longitudinal), –0.5 angular Turbid mating cycling Wetmating test > 100 mating cycles at 5,000psig in simulated silty seawater (2 to 500 m particle size) at 36 –3 F (2 –2 C). Flooded connector capability Flooded connector cable termination test...
Open the catalog to page 3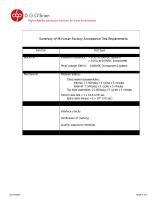
Summary of Minimum Factory Acceptance Test Requirements Function Electrical Test Type Insulation resistance Proof voltage (DWV) - 2400VDC (component & system) Mechanical Pressure testing Glass sealed subassemblies: - Internal: 17,500psig x 5 cycles x 5 minutes - External: 7,500psig x 5 cycles x 5 minutes Top level assemblies: 15,000psig x 5 cycles x 5 minutes Helium leak test < 1 x 10-6 cm3/sec (glass seals always < 1 x 10-8 cm3/sec) Quality conformance Tolerance checks Interface checks Verification of marking Quality assurance checklists Packaging and preservation
Open the catalog to page 4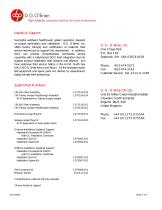
Logistical Support: Successful wellhead feedthrough system operation depends on proper termination and installation. D.G. O Brien, Inc. offers factory training and certification of customer field service technicians to support this requirement. In addition, DGO can provide comprehensive world-wide service capability with a fully-trained DGO field integration team to support product installation both onshore and offshore. We have extensive field service history in the GOM, North Sea (UK & NCS), West Africa and Brazil. All the necessary tools, test equipment and spare parts are utilized by...
Open the catalog to page 5All Teledyne D.G.O'Brien catalogs and brochures
-
Single Pin Horizontal EFS
2 Pages
-
Omicron
5 Pages
-
Nautilus WM10-250
2 Pages
-
Nautilus™ WM1.7-60
2 Pages
-
FACT
2 Pages
-
Compact FACT
2 Pages
-
100 Series Connector
2 Pages
-
110 Series Coaxial Connector
2 Pages
-
107 Series Connector
1 Pages
Archived catalogs
-
Sentinel V
4 Pages
-
Pinnacle 45
2 Pages
-
ChannelMaster
4 Pages
-
Teledyne Marine Vehicles
24 Pages
-
Saturn INS
2 Pages
-
LED-V-Series
2 Pages
-
UTS-9400
2 Pages
-
RiverPro ADCP
2 Pages
-
RiverRay ADCP
2 Pages
-
DGO 108 Series Connectors
2 Pages
-
DGO Product Selection Guide
5 Pages
-
ODI FACT
2 Pages
-
ODI Nautilus WM10-250
2 Pages
-
DGO Standard Products Catalog
25 Pages
-
ODI Extended Ethernet
1 Pages
-
ODI Hybrid FACT
1 Pages
-
PDM QuickCure Molding System
1 Pages
-
Storm Cable Capabilities
1 Pages
-
Penetrators and Feedthroughs
1 Pages
-
Product catalog:DGOstdcat
34 Pages