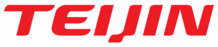

Catalog excerpts
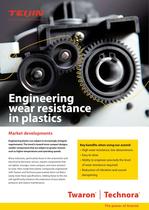
wear resistance Market developments Engineering plastics are subject to increasingly stringent requirements. The trend is toward more compact designs, smaller components that are subject to greater stresses such as higher temperatures and operating speeds. Many industries, particularly those in the automotive and electrical & electronic sectors, require components that are lighter, stronger, more compact, and more resistant to wear. Parts made from plastic compounds engineered withTwaron andTechnora para-aramid short-cut fibers easily meet these specifications. Adding these to the mix will significantly enhance the endurance of your plastic products and reduce maintenance. Key benefits when using our aramid • High wear resistance, low abrasiveness • Ability to engineer precisely the level of wear resistance required • Reduction of vibration and sound
Open the catalog to page 1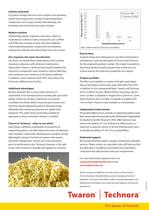
Industry demands As product designs become more compact and operating speeds and temperatures increase, engineering plastic components such as gear wheels, slide bearings and bushings need to be extremely wear-resistant. Modern solution Traditionally, plastics engineers used glass, carbon or molybdenum sulfide to make compounds such as PA66 and POM more resistant to wear. But these additives make engineering plastic compounds more abrasive, eroding the materials with which they come into contact. Our response: less wear, less abrasion Our short-cut aramid fibers create plastics that combine...
Open the catalog to page 2All TEIJIN ARAMID BV catalogs and brochures
-
Leaflet-Marine
2 Pages
-
Ballistic Material Handbook
11 Pages
-
Twaron-product-brochure
7 Pages
-
Optical-fiber-cables-leaflet
2 Pages
-
Leaflet-Twaron-Tape_final-LR
2 Pages
-
Leaflet-special-paper-v2
2 Pages
-
Leaflet-Staple-fibre_Engels
2 Pages
-
Leaflet-Twaron-Black_lowres
2 Pages
Archived catalogs
-
Properties-of-Twaron
1 Pages