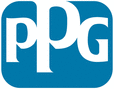
Catalog excerpts
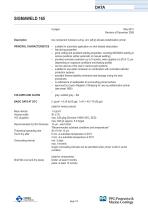
two component moisture curing, zinc (ethyl) silicate prefabrication primer PRINCIPAL CHARACTERISTICS – suitable for automatic application on shot blasted steel plates – fast drying properties – good cutting and excellent welding properties, including MIG/MAG welding in various positions (either automatic or manual welding) – provides corrosion protection up to 9 months, when applied at a dft of 13 μm (depending on exposure conditions and blasting prole) – can be used as a rst coat in various paint systems – suitable for sea water immersion in combination with controlled cathodic protection systems – excellent thermal stability minimizes heat damage during hot work procedures – no adherence of weldspatter at surrounding primed surface – approved by Lloyd's Register of Shipping for use as prefabrication primer (see sheet 1880) – COLOURS AND GLOSS grey, reddish grey – at BASIC DATA AT 20°C (1 g/cm³ = 8.35 lb/US gal; 1 m²/l = 40.7 ft²/US gal) (data for mixed product) Mass density Volume solids VOC (Supplied) Recommended dry lm thickness Theoretical spreading rate Touch dry after Overcoating interval Shelf life (cool and dry place) 1.4 g/cm³ 30 ± 2% max. 428 g/kg (Directive 1999/13/EC, SED) max. 645 g/l (approx. 5.4 lb/gal) 13 μm - see further: "Recommended substrate conditions and temperatures" 20 m²/l for 13 μm 6 min. at substrate temperature of 20°C 3 min. at a substrate temperature of 40°C min. 3 days max. 9 months longer overcoating intervals can be permitted when primer is still in sound condition (data for components) binder: at least 9 months paste: at least 12 months
Open the catalog to page 1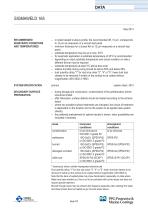
RECOMMENDED SUBSTRATE CONDITIONS AND TEMPERATURES – on steel blasted to above prole, the recommended dft, 13 μm, corresponds to 15 μm as measured on a smooth test panel – minimum thickness for a closed lm is 13 μm measured on a smooth test panel – substrate temperature may be up to max. 50°C – for automatic application a substrate temperature of 30°C is recommended – depending on exact substrate temperature and actual condition on side a different thinner may be required – substrate temperature at least 3°C above dew point – relative humidity during curing should be above 50% and below 85%...
Open the catalog to page 2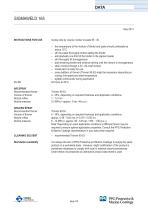
mixing ratio by volume: binder to paste 55 : 45 – the temperature of the mixture of binder and paste should preferably be above 15°C – stir the paste thoroughly before adding the binder – add gradually one third of the binder to the pigment paste – stir thoroughly till homogeneous – add remaining binder and continue stirring until the mixture is homogeneous – strain mixture through a 30 - 60 mesh screen – mixed paint is ready for use – some addition of thinner (Thinner 90-53) might be necessary depending on routing, line speed and steel temperature – agitate continuously during application...
Open the catalog to page 3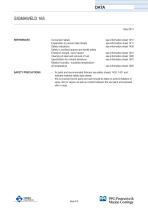
SAFETY PRECAUTIONS Conversion tabels Explanation to product data sheets Safety indications Safety in conned spaces and health safety Explosion hazard - toxic hazard Cleaning of steel and removal of rust Specication for mineral abrasives Relative humidity - substrate temperature air temperature see information sheet 1410 see information sheet 1411 see information sheet 1430 see information sheet 1431 see information sheet 1490 see information sheet 1491 see information sheet 1650 – for paint and recommended thinners see safety sheets 1430, 1431 and relevant material safety data sheets – this...
Open the catalog to page 4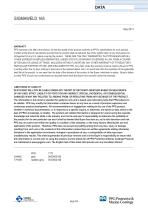
WARRANTY PPG warrants (i) its title to the product, (ii) that the quality of the product conforms to PPG’s specications for such product in effect at the time of manufacture and (iii) that the product shall be delivered free of the rightful claim of any third person for infringement of any U.S. patent covering the product. THESE ARE THE ONLY WARRANTIES THAT PPG MAKES AND ALL OTHER EXPRESS OR IMPLIED WARRANTIES, UNDER STATUTE OR ARISING OTHERWISE IN LAW, FROM A COURSE OF DEALING OR USAGE OF TRADE, INCLUDING WITHOUT LIMITATION, ANY OTHER WARRANTY OF FITNESS FOR A PARTICULAR PURPOSE OR USE,...
Open the catalog to page 5All Sigma Coatings PPG PMC catalogs and brochures
-
SIGMAGLIDE® 890
2 Pages
-
PPG STEELGUARD™
5 Pages
-
PPG PSX® 700
5 Pages
-
SIGMAPRIME
8 Pages
-
PPG Hydroelectric power
4 Pages
-
PPG HI-TEMP 900
2 Pages
-
PPG FPSO
4 Pages
-
PPG Fossil power
4 Pages
-
PPG Drill ships
4 Pages
-
PITT-CHAR® XP
5 Pages
-
AMERSHIELD®
4 Pages
-
AMERLOCK® SERIES
4 Pages
-
AMERCOAT 240 SERIES
4 Pages
-
SIGMACOVER 280
7 Pages
-
SIGMAWELD™ 120
4 Pages
-
SIGMASHIELD 1200
5 Pages
-
PSX® 700
8 Pages
-
AMERCOAT 205
5 Pages
-
AMERCOAT 114 A
5 Pages
-
ABC 4
4 Pages
-
ABC 3
4 Pages
-
AMERCOAT 242 HB
6 Pages
-
AMERCOAT 242
6 Pages
-
AMERCOAT 238
6 Pages
-
AMERCOAT 237 M
5 Pages
-
AMERCOAT 138 G
5 Pages
-
SIGMASHIELD 1090
5 Pages
-
SIGMASHIELD 1200
5 Pages
-
SIGMATHERM 500
3 Pages
-
SIGMAWELD 190
5 Pages
-
SIGMATHERM 540
3 Pages
-
NOVAGUARD 840
5 Pages
-
SIGMA ECOFLEET® 690
2 Pages
-
PHENGUARD 935 EN
5 Pages
-
SIGMA ALPHAGEN 240 EN
5 Pages
-
SIGMACOVER 435 EN
6 Pages
-
SIGMADUR 580 EN
4 Pages
-
SIGMAGUARD 720 EN
4 Pages
-
SIGMADUR ONE
3 Pages
-
SIGMAGLIDE 990
3 Pages
-
SIGMAGUARD CSF 650
6 Pages
-
SIGMARINE 42
2 Pages
-
SIGMAZINC 102
4 Pages
-
SIGMAWELD 199
4 Pages
-
SIGMA VIKOTE 18
3 Pages
-
SIGMATHERM 175
2 Pages
-
SIGMASHIELD 420 LT
4 Pages
-
SIGMARINE 28
3 Pages
-
SIGMAGUARD 425
4 Pages
-
SIGMA ECOFLEET 238 A
3 Pages
-
SIGMADUR 500US
4 Pages
-
SIGMACOVER 520
4 Pages
-
SIGMACOVER 380
4 Pages
-
SIGMA AQUACOVER 45
3 Pages
-
SIGMA ALPHAGEN 230
5 Pages
-
PHENGUARD 930
5 Pages