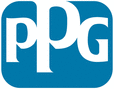
Catalog excerpts
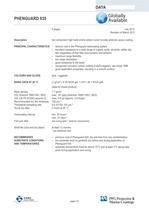
PHENGUARD 935 5 pages Description July 2012 Revision of March 2011 two component high build amine adduct cured novolac phenolic epoxy coating PRINCIPAL CHARACTERISTICS – second coat in the Phenguard tankcoating system – excellent resistance to a wide range of organic acids, alcohols, edible oils, fats (regardless of free fatty acid content) and solvents – maximum cargo exibility – low cargo absorption – good resistance to hot water – recognized corrosion control coating (Lloyd's register), see sheet 1886 – good application properties, resulting in a smooth surface COLOURS AND GLOSS pink – eggshell BASIC DATA AT 20 °C (1 g/cm³ = 8.35 lb/US gal; 1 m²/l = 40.7 ft²/US gal) (data for mixed product) Mass density VOC (Directive 1999/13/EC, SED) VOC (UK PG 6/23(92) appendix 3) Recommended dry lm thickness Theoretical spreading rate Touch dry after 1.7 g/cm³ max. 191 g/kg (Directive 1999/13/EC, SED) max. 315 g/l (approx. 2.6 lb/gal) 100 μm * 6.6 m²/l for 100 μm * 2 hours at 20 °C Overcoating interval min. 24 hours * max. 21 days * Full cure after see curing table * (data for components) Shelf life (cool and dry place) at least 12 months * see additional data RECOMMENDED SUBSTRATE CONDITIONS AND TEMPERATURES – previous coat of Phenguard 930; dry and free from any contamination – the substrate must be perfectly dry before and during application of Phenguard 935 – substrate temperature must be above 10°C and at least 3°C above dew point during application and curing page 1/5
Open the catalog to page 1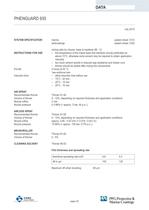
PHENGUARD 935 July 2012 SYSTEM SPECIFICATION INSTRUCTIONS FOR USE Pot life marine tankcoatings system sheet: 3141 system sheet: 3322 mixing ratio by volume: base to hardener 88 : 12 – the temperature of the mixed base and hardener should preferably be above 15°C, otherwise extra solvent may be required to obtain application viscosity – too much solvent results in reduced sag resistance and slower cure – thinner should be added after mixing the components 4 hours at 20 °C *see additional data Induction time – – – – allow induction time before use 15°C - 20 min. 20°C - 15 min. 25°C - 10 min....
Open the catalog to page 2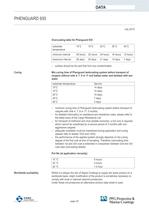
PHENGUARD 935 July 2012 Overcoating table for Phenguard 935 substrate temperature 10°C 15°C 20°C minimum interval 36 hours 32 hours 24 hours 16 hours 12 hours maximum interval 28 days 25 days 21 days 30°C 14 days 40°C 7 days – surface should be dry and free from any contamination Curing Min.curing time of Phenguard tankcoating system before transport of cargoes without note 4, 7, 8 or 11 and ballast water and tanktest with sea water substrate temperature 10°C 15°C 20°C 30°C 40°C Service 14 days 14 days 10 days 7 days 5 days – minimum curing time of Phenguard tankcoating system before...
Open the catalog to page 3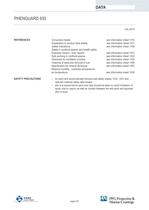
PHENGUARD 935 July 2012 REFERENCES SAFETY PRECAUTIONS Conversion tabels Explanation to product data sheets Safety indications Safety in conned spaces and health safety Explosion hazard - toxic hazard Safe working in conned spaces Directives for ventilation practice Cleaning of steel and removal of rust Specication for mineral abrasives Relative humidity - substrate temperature air temperature see information sheet 1410 see information sheet 1411 see information sheet 1430 see information sheet 1431 see information sheet 1433 see information sheet 1434 see information sheet 1490 see...
Open the catalog to page 4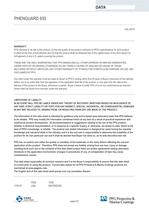
PHENGUARD 935 July 2012 WARRANTY PPG warrants (i) its title to the product, (ii) that the quality of the product conforms to PPG’s specications for such product in effect at the time of manufacture and (iii) that the product shall be delivered free of the rightful claim of any third person for infringement of any U.S. patent covering the product. THESE ARE THE ONLY WARRANTIES THAT PPG MAKES AND ALL OTHER EXPRESS OR IMPLIED WARRANTIES, UNDER STATUTE OR ARISING OTHERWISE IN LAW, FROM A COURSE OF DEALING OR USAGE OF TRADE, INCLUDING WITHOUT LIMITATION, ANY OTHER WARRANTY OF FITNESS FOR A...
Open the catalog to page 5All Sigma Coatings PPG PMC catalogs and brochures
-
SIGMAGLIDE® 890
2 Pages
-
PPG STEELGUARD™
5 Pages
-
PPG PSX® 700
5 Pages
-
SIGMAPRIME
8 Pages
-
PPG Hydroelectric power
4 Pages
-
PPG HI-TEMP 900
2 Pages
-
PPG FPSO
4 Pages
-
PPG Fossil power
4 Pages
-
PPG Drill ships
4 Pages
-
PITT-CHAR® XP
5 Pages
-
AMERSHIELD®
4 Pages
-
AMERLOCK® SERIES
4 Pages
-
AMERCOAT 240 SERIES
4 Pages
-
SIGMACOVER 280
7 Pages
-
SIGMAWELD™ 120
4 Pages
-
SIGMASHIELD 1200
5 Pages
-
PSX® 700
8 Pages
-
AMERCOAT 205
5 Pages
-
AMERCOAT 114 A
5 Pages
-
ABC 4
4 Pages
-
ABC 3
4 Pages
-
AMERCOAT 242 HB
6 Pages
-
AMERCOAT 242
6 Pages
-
AMERCOAT 238
6 Pages
-
AMERCOAT 237 M
5 Pages
-
AMERCOAT 138 G
5 Pages
-
SIGMASHIELD 1090
5 Pages
-
SIGMASHIELD 1200
5 Pages
-
SIGMATHERM 500
3 Pages
-
SIGMAWELD 165
5 Pages
-
SIGMAWELD 190
5 Pages
-
SIGMATHERM 540
3 Pages
-
NOVAGUARD 840
5 Pages
-
SIGMA ECOFLEET® 690
2 Pages
-
SIGMA ALPHAGEN 240 EN
5 Pages
-
SIGMACOVER 435 EN
6 Pages
-
SIGMADUR 580 EN
4 Pages
-
SIGMAGUARD 720 EN
4 Pages
-
SIGMADUR ONE
3 Pages
-
SIGMAGLIDE 990
3 Pages
-
SIGMAGUARD CSF 650
6 Pages
-
SIGMARINE 42
2 Pages
-
SIGMAZINC 102
4 Pages
-
SIGMAWELD 199
4 Pages
-
SIGMA VIKOTE 18
3 Pages
-
SIGMATHERM 175
2 Pages
-
SIGMASHIELD 420 LT
4 Pages
-
SIGMARINE 28
3 Pages
-
SIGMAGUARD 425
4 Pages
-
SIGMA ECOFLEET 238 A
3 Pages
-
SIGMADUR 500US
4 Pages
-
SIGMACOVER 520
4 Pages
-
SIGMACOVER 380
4 Pages
-
SIGMA AQUACOVER 45
3 Pages
-
SIGMA ALPHAGEN 230
5 Pages
-
PHENGUARD 930
5 Pages