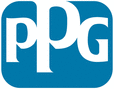
Catalog excerpts
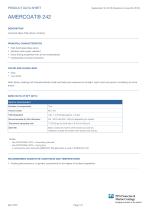
PRODUCT DATA SHEET September 18, 2015 (Revision of June 28, 2015) AMERCOAT® 242 DESCRIPTION Universal Glass Flake Epoxy Coating PRINCIPAL CHARACTERISTICS • High build glass flake epoxy • Abrasion and impact resistant • Good drying properties even at low temperatures • Outstanding corrosion protection COLOR AND GLOSS LEVEL • Gray • Low sheen Note: Epoxy coatings will characteristically chalk and fade upon exposure to sunlight. Light colors are prone to ambering to some extent BASIC DATA AT 68°F (20°C) Data for mixed product Number of components Volume solids Recommended dry film thickness 8.0 - 20.0 mils (200 - 500 µm) depending on system Theoretical spreading rate Shelf life Base: at least 24 months when stored cool and dry Hardener: at least 36 months when stored cool and dry Notes: - See ADDITIONAL DATA – Overcoating intervals - See ADDITIONAL DATA – Curing time - 3 components when post-add AMERCOAT 880 glass flake is used in AMERCOAT 240 RECOMMENDED SUBSTRATE CONDITIONS AND TEMPERATURES • Coating performance is, in general, proportional to the degree of surface preparation
Open the catalog to page 1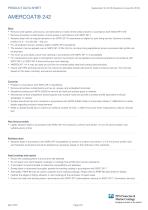
PRODUCT DATA SHEET September 18, 2015 (Revision of June 28, 2015) AMERCOAT® 242 Steel • Remove weld spatter, protrusions, and laminations in steel. Grind welds smooth in accordance with NACE RP-0178 • Remove all surface contaminants, oil and grease in accordance with SSPC SP-1 • Abrasive blast with an angular abrasive to an SSPC SP-10 cleanliness or higher for tank lining service. Achieve a surface profile of 2.0 – 4.0 mils (50 – 100 µm) • For atmospheric service, abrasive blast to SSPC SP-6 standards • The product may be applied over an SSPC SP-12 WJ-2(L) for non-tank lining applications...
Open the catalog to page 2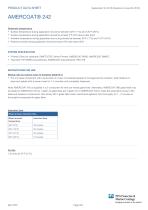
PRODUCT DATA SHEET September 18, 2015 (Revision of June 28, 2015) AMERCOAT® 242 Substrate temperature • Surface temperature during application should be between 20°F (-7°C) and 120°F (49°C) • Surface temperature during application should be at least 5°F (3°C) above dew point • Ambient temperature during application and curing should be between 20°F (-7°C) and 110°F (43°C) • Relative humidity during application should be above 0% and below 85% SYSTEM SPECIFICATION • Primers: Direct to substrate; DIMETCOTE- Series Primers, AMERCOAT 68HS, AMERCOAT 68MCZ • Topcoats: PITTHANE polyurethanes,...
Open the catalog to page 3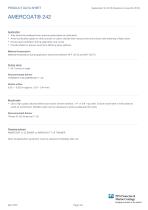
PRODUCT DATA SHEET September 18, 2015 (Revision of June 28, 2015) AMERCOAT® 242 Application • Area should be sheltered from airborne particulates and pollutants • Avoid combustion gases or other sources of carbon dioxide that may promote amine blush and ambering of light colors • Ensure good ventilation during application and curing • Provide shelter to prevent wind from affecting spray patterns Material temperature Material temperature during application should be between 50°F (10°C) and 90°F (32°C) Airless spray • 64:1 pump or larger Recommended thinner THINNER 91-82 (AMERCOAT T-10)...
Open the catalog to page 4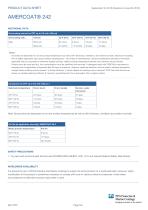
PRODUCT DATA SHEET September 18, 2015 (Revision of June 28, 2015) AMERCOAT® 242 ADDITIONAL DATA Overcoating interval for DFT up to 6.0 mils (150 µm) Overcoating with... Notes: - Dry times are dependent on air and surface temperatures as well as film thickness, ventilation, and relative humidity. Maximum recoating time is highly dependent upon actual surface temperatures – not simply air temperatures. Surface temperatures should be monitored, especially with sun-exposed or otherwise heated surfaces. Higher surface temperatures shorten the maximum recoat window - Surface must be clean and...
Open the catalog to page 5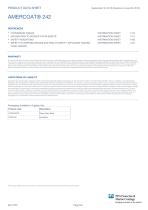
PRODUCT DATA SHEET September 18, 2015 (Revision of June 28, 2015) AMERCOAT® 242 REFERENCES • CONVERSION TABLES • EXPLANATION TO PRODUCT DATA SHEETS • SAFETY INDICATIONS • SAFETY IN CONFINED SPACES AND HEALTH SAFETY, EXPLOSION HAZARD – INFORMATION SHEET INFORMATION SHEET INFORMATION SHEET INFORMATION SHEET TOXIC HAZARD WARRANTY PPG warrants (i) its title to the product, (ii) that the quality of the product conforms to PPG’s specifications for such product in effect at the time of manufacture and (iii) that the product shall be delivered free of the rightful claim of any third person for...
Open the catalog to page 6All Sigma Coatings PPG PMC catalogs and brochures
-
SIGMAGLIDE® 890
2 Pages
-
PPG STEELGUARD™
5 Pages
-
PPG PSX® 700
5 Pages
-
SIGMAPRIME
8 Pages
-
PPG Hydroelectric power
4 Pages
-
PPG HI-TEMP 900
2 Pages
-
PPG FPSO
4 Pages
-
PPG Fossil power
4 Pages
-
PPG Drill ships
4 Pages
-
PITT-CHAR® XP
5 Pages
-
AMERSHIELD®
4 Pages
-
AMERLOCK® SERIES
4 Pages
-
AMERCOAT 240 SERIES
4 Pages
-
SIGMACOVER 280
7 Pages
-
SIGMAWELD™ 120
4 Pages
-
SIGMASHIELD 1200
5 Pages
-
PSX® 700
8 Pages
-
AMERCOAT 205
5 Pages
-
AMERCOAT 114 A
5 Pages
-
ABC 4
4 Pages
-
ABC 3
4 Pages
-
AMERCOAT 242 HB
6 Pages
-
AMERCOAT 238
6 Pages
-
AMERCOAT 237 M
5 Pages
-
AMERCOAT 138 G
5 Pages
-
SIGMASHIELD 1090
5 Pages
-
SIGMASHIELD 1200
5 Pages
-
SIGMATHERM 500
3 Pages
-
SIGMAWELD 165
5 Pages
-
SIGMAWELD 190
5 Pages
-
SIGMATHERM 540
3 Pages
-
NOVAGUARD 840
5 Pages
-
SIGMA ECOFLEET® 690
2 Pages
-
PHENGUARD 935 EN
5 Pages
-
SIGMA ALPHAGEN 240 EN
5 Pages
-
SIGMACOVER 435 EN
6 Pages
-
SIGMADUR 580 EN
4 Pages
-
SIGMAGUARD 720 EN
4 Pages
-
SIGMADUR ONE
3 Pages
-
SIGMAGLIDE 990
3 Pages
-
SIGMAGUARD CSF 650
6 Pages
-
SIGMARINE 42
2 Pages
-
SIGMAZINC 102
4 Pages
-
SIGMAWELD 199
4 Pages
-
SIGMA VIKOTE 18
3 Pages
-
SIGMATHERM 175
2 Pages
-
SIGMASHIELD 420 LT
4 Pages
-
SIGMARINE 28
3 Pages
-
SIGMAGUARD 425
4 Pages
-
SIGMA ECOFLEET 238 A
3 Pages
-
SIGMADUR 500US
4 Pages
-
SIGMACOVER 520
4 Pages
-
SIGMACOVER 380
4 Pages
-
SIGMA AQUACOVER 45
3 Pages
-
SIGMA ALPHAGEN 230
5 Pages
-
PHENGUARD 930
5 Pages