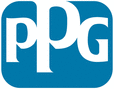
Catalog excerpts
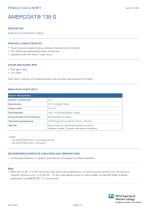
PRODUCT DATA SHEET AMERCOAT® 138 G DESCRIPTION Heavy duty non-skid epoxy coating PRINCIPAL CHARACTERISTICS • Tough, abrasion resistant epoxy coating containing hard non-skid grit • Non-skid grit pre-dispersed in epoxy component • Qualified to Mil-PRF-24667, Types I and 2 COLOR AND GLOSS LEVEL • Dark gray, black • Low sheen Note: Epoxy coatings will characteristically chalk and fade upon exposure to sunlight BASIC DATA AT 68°F (20°C) Data for mixed product Number of components Mass density Volume solids Recommended dry film thickness See spreading rate tables Theoretical spreading rate Shelf life Base: at least 12 months when stored cool and dry Hardener: at least 12 months when stored cool and dry Notes: - See ADDITIONAL DATA – Overcoating intervals - See ADDITIONAL DATA – Curing time RECOMMENDED SUBSTRATE CONDITIONS AND TEMPERATURES • Coating performance is, in general, proportional to the degree of surface preparation Steel • SSPC SP-10, SP-11, or SP-12 WJ-2(L), then prime with suitable primer. A minimum anchor profile of 2.0 mils (50 µm) is required. Optimum is 3.0 – 4.5 mils (75 – 114 µm). See specific primer for further details. For Mil-PRF-24667 qualified applications, use AMERCOAT 137 as the primer
Open the catalog to page 1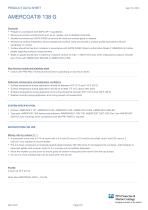
PRODUCT DATA SHEET AMERCOAT® 138 G Concrete • Prepare in accordance with SSPC SP-13 guidelines • Remove all surface contaminants such as oil, grease, and embedded chemicals • Abrade the surface per ASTM D4259 to remove all chalk and surface glaze or laitance • Mechanical surface preparation should expose sub-surface voids and provide a surface profile equivalent to 60 grit sandpaper or coarser • Surface should be free from moisture in accordance with ASTM D4263. Refer to Information Sheet # 1496ACUS for further details regarding moisture measurements • Slabs on grade should have a maximum...
Open the catalog to page 2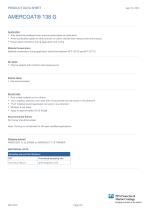
PRODUCT DATA SHEET AMERCOAT® 138 G Application • Area should be sheltered from airborne particulates and pollutants • Avoid combustion gases or other sources of carbon dioxide that may promote amine blush. • Ensure good ventilation during application and curing Material temperature Material temperature during application should be between 60°F (16°C) and 80°F (27°C) Air spray • May be applied with a bottom feed pressure pot Airless spray • Not recommended Brush/roller • Pour mixed material out in a ribbon • Use a napless, phenolic core roller with a long handle and roll evenly in one...
Open the catalog to page 3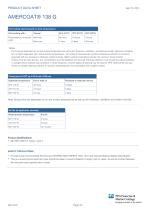
PRODUCT DATA SHEET AMERCOAT® 138 G Overcoating interval based on deck temperatures Overcoating with... Notes: - Dry times are dependent on air and surface temperatures as well as film thickness, ventilation, and relative humidity. Maximum recoating time is highly dependent upon actual surface temperatures – not simply air temperatures. Surface temperatures should be monitored, especially with sun-exposed or otherwise heated surfaces. Higher surface temperatures shorten the maximum recoat window - Surface must be clean and dry. Any contamination must be identified and removed. Particular...
Open the catalog to page 4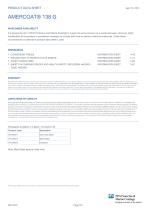
PRODUCT DATA SHEET AMERCOAT® 138 G WORLDWIDE AVAILABILITY It is always the aim of PPG Protective and Marine Coatings to supply the same product on a worldwide basis. However, slight modification of the product is sometimes necessary to comply with local or national rules/circumstances. Under these circumstances an alternative product data sheet is used. REFERENCES • CONVERSION TABLES • EXPLANATION TO PRODUCT DATA SHEETS • SAFETY INDICATIONS • SAFETY IN CONFINED SPACES AND HEALTH SAFETY, EXPLOSION HAZARD – INFORMATION SHEET INFORMATION SHEET INFORMATION SHEET INFORMATION SHEET TOXIC HAZARD...
Open the catalog to page 5All Sigma Coatings PPG PMC catalogs and brochures
-
SIGMAGLIDE® 890
2 Pages
-
PPG STEELGUARD™
5 Pages
-
PPG PSX® 700
5 Pages
-
SIGMAPRIME
8 Pages
-
PPG Hydroelectric power
4 Pages
-
PPG HI-TEMP 900
2 Pages
-
PPG FPSO
4 Pages
-
PPG Fossil power
4 Pages
-
PPG Drill ships
4 Pages
-
PITT-CHAR® XP
5 Pages
-
AMERSHIELD®
4 Pages
-
AMERLOCK® SERIES
4 Pages
-
AMERCOAT 240 SERIES
4 Pages
-
SIGMACOVER 280
7 Pages
-
SIGMAWELD™ 120
4 Pages
-
SIGMASHIELD 1200
5 Pages
-
PSX® 700
8 Pages
-
AMERCOAT 205
5 Pages
-
AMERCOAT 114 A
5 Pages
-
ABC 4
4 Pages
-
ABC 3
4 Pages
-
AMERCOAT 242 HB
6 Pages
-
AMERCOAT 242
6 Pages
-
AMERCOAT 238
6 Pages
-
AMERCOAT 237 M
5 Pages
-
SIGMASHIELD 1090
5 Pages
-
SIGMASHIELD 1200
5 Pages
-
SIGMATHERM 500
3 Pages
-
SIGMAWELD 165
5 Pages
-
SIGMAWELD 190
5 Pages
-
SIGMATHERM 540
3 Pages
-
NOVAGUARD 840
5 Pages
-
SIGMA ECOFLEET® 690
2 Pages
-
PHENGUARD 935 EN
5 Pages
-
SIGMA ALPHAGEN 240 EN
5 Pages
-
SIGMACOVER 435 EN
6 Pages
-
SIGMADUR 580 EN
4 Pages
-
SIGMAGUARD 720 EN
4 Pages
-
SIGMADUR ONE
3 Pages
-
SIGMAGLIDE 990
3 Pages
-
SIGMAGUARD CSF 650
6 Pages
-
SIGMARINE 42
2 Pages
-
SIGMAZINC 102
4 Pages
-
SIGMAWELD 199
4 Pages
-
SIGMA VIKOTE 18
3 Pages
-
SIGMATHERM 175
2 Pages
-
SIGMASHIELD 420 LT
4 Pages
-
SIGMARINE 28
3 Pages
-
SIGMAGUARD 425
4 Pages
-
SIGMA ECOFLEET 238 A
3 Pages
-
SIGMADUR 500US
4 Pages
-
SIGMACOVER 520
4 Pages
-
SIGMACOVER 380
4 Pages
-
SIGMA AQUACOVER 45
3 Pages
-
SIGMA ALPHAGEN 230
5 Pages
-
PHENGUARD 930
5 Pages