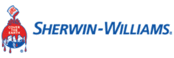
Catalog excerpts

SHER-RELEASE SYSTEM Protective & Marine Coatings SEAGUARD® SURFACE COAT PART A PART B P31-200 SERIES P31V-200 SERIES Revised 7/11 9.57 PRODUCT DESCRIPTION RECOMMENDED USES SeaGuard Surface Coat is a silicone based, biocide free, topcoat in the Sher-Release System. The low surface energy provides excellent foul release properties. The SeaGuard Surface Coat provides superior durability as compared to traditional silicone foul release systems. • • • Provides owners with rapid return on investment due to reduction in fuel consumption. • • • PRODUCT CHARACTERISTICS • Finish: Semi-Gloss Color: Black, Red, White and Blue Volume solids (ASTM D2697 modied): 80% (± 2%) Components: 2 Mixing ratio (by volume) • PERFORMANCE CHARACTERISTICS The Sher-Release System has been analyzed through the following test methods. For specic test results consult your Sherwin Williams representative. ~4:1 (Part A to Part B) VOC as Applied (Theoretical): 1.24 lb/gal 149 g/L Recommended Spreading Rate per coat: Wet mils (microns) Dry mils (microns) ~Coverage sq ft/gal (m2/L) Theoretical coverage sq ft/gal (m2/L) @ 1 mil / 25 microns dft Where long-life fouling protection in severe service is required Where reduction in operating costs and extended drydocking intervals is desirable Suitable for most vessels in a wide range of operating environments trading at >10 knots For lower operating speeds, please inquire Container ships, cruise vessels, Ro-Ro's, tankers, etc. Structures and operating equipment including intake tunnels and tubes, trash racks, gates, water boxes, service water systems, etc. Industrial or municipal facilities with high water usage including Power Generation, Water Treatment, and Pulp & Paper. Please consult your local Sherwin-Williams Technical Representative prior to using on vessels with cooling coils or cooling equipment positioned on submerged hull exteriors due to the coating system's insulating effects. Minimum 8.0 (200) 6.0 (150) 214 (5.27) Maximum • Standard practice for surface wettability of coatings, substrates and pigments by advancing contact angle measurement (ASTM D744408): • Standard test method for surface wettability and absorbency of sheeted materials using an automated contact angle tester (ASTM D5725-99): 1283 (31.6) Drying Schedule @ 6.0 mils wet (150 microns): • Standard test method for measuring adhesion of organic coatings to plastic substrates by direct tensile testing (ASTM D5179-02): @ @ 40°F/4.5°C 50°F/10°C @ 75°F/24°C @ 90°F/32°C • Standard test method for specular gloss at 60° (ASTM D523-89): 48 hours 24 hours 24 hours • Standard test method for measurement of barnacle adhesion strength in shear (ASTM D5618-94): If the maximum recoat window interval is exceeded, consult your Sherwin-Williams representative for corrective procedures. Drying time is temperature, humidity, and lm thickness dependent. Pot Life: 1 hour @ 75°F/24°C • Standard test method for scratch hardness of materials using a diamond stylus (ASTM G171-03): Before immersion: 36 hours Sweat-in-Time: None required Shelf Life: 12 months, unopened Store indoors out of direct sunlight at 40°F (4.5°C) to 80°F (27°C) 93°F (34°C) SETA Not normally required. If necessary, thin up to maximum of 3 ounces per gallon using VM&P Naphtha R1K3. VM&P Naphtha R1K3 Flash Point: Reducer: Clean Up: • Standard test method for apparent shear strength of single-lap-joint adhesively bonded metal specimens by tension loading (metal-to-metal) (ASTM D1002-03): • Standard test method for abrasion resistance of organic coatings by the taber abraser (ASTM D4060-07): • Standard test method for adhesion of organic coatings by scrape adhesion (ASTM D2197-98): www.sherwin-williams.com/protective continued on back
Open the catalog to page 1
SHER-RELEASE SYSTEM Protective & Marine Coatings SEAGUARD® SURFACE COAT PART A PART B P31-200 SERIES P31V-200 SERIES PRODUCT INFORMATION SURFACE PREPARATION RECOMMENDED SYSTEMS Dry Film Thickness / ct. Mils (Microns) Recommended MARINE systems for Sher-Release System: Steel, Immersion: 1 ct.. SeaGuard 6100 Epoxy 1 ct. SeaGuard 6100 Epoxy 1 ct. SeaGuard Tie Coat 1 ct. SeaGuard Surface Coat Aluminum, Immersion: 1 ct. SeaGuard MP Epoxy or 1 ct. SeaGuard 6100 Epoxy 1 ct. SeaGuard 6100 Epoxy 1 ct. SeaGuard Tie Coat 1 ct. SeaGuard Surface Coat Fiberglass, Immersion: 1 ct.. SeaGuard 6100 Epoxy 1...
Open the catalog to page 2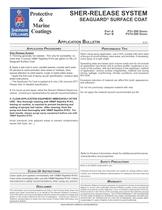
SHER-RELEASE SYSTEM Protective & Marine Coatings SEAGUARD® SURFACE COAT PART A PART B P31-200 SERIES P31V-200 SERIES APPLICATION BULLETIN APPLICATION PROCEDURES Sher-Release System 1. Thinning generally not needed. Thin only for workability; no more than 3 ounces VM&P Naphtha R1K3 per gallon (3.78L) of Seaguard Surface Coat. 9.57 PERFORMANCE TIPS When using spray application, use a 50% overlap with each pass of the gun to avoid holidays, bare areas, and pinholes. If necessary, cross spray at a right angle Spreading rates are based upon volume solids and do not include an application loss...
Open the catalog to page 4All Sherwin-Williams catalogs and brochures
-
N51R301 / N51B301
4 Pages
-
TT-P-645C
4 Pages
-
Fast Clad® ER Epoxy
4 Pages
-
TT-P-645B
4 Pages
-
TANKGUARD® EPOXY POLYAMIDE
4 Pages
-
SEAGUARD® 1000 MARINE ENAMEL
4 Pages
-
MIL-DTL-24441/19C TYPE III
4 Pages
-
FAST CLAD® BRUSH GRADE EPOXY
4 Pages
-
ANTI-GRAFFITI COATING
4 Pages
-
EURONAVY ES301L / ES301K
4 Pages
-
FAST CLAD® EPOXY PRIMER
4 Pages
-
SEAGUARD VOID COAT
2 Pages