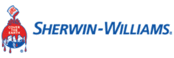
Catalog excerpts
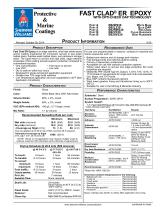
Fast Clad® ER Technology Epoxy With OPTI-Check OAP Protective & Marine Coatings Part A Part A Part A Part B Part B B62W230 White Base B62L230 Blue OAP B62RW230 Red Oxide B62V230 Clear Hardener B62AV230 Gray Hardener Product Description Fast Clad ER Epoxy is an edge retentive, ultra high solids epoxy amine coating engineered for immersion service in sea water ballast tanks, fuel/sea water ballast tanks, and petroleum storage tanks. The rapid return to service and high build, edge retentive properties of this coating provide superior protection compared to conventional epoxies. • One coat protection • Fast return to service • Low VOC • Low odor • Dry to walk-on within four hours • Designed for plural-component application equipment • Greater than 70% edge build retention • Low Temperature application and cure capabilities to 35°F (See Application Conditions) Product Characteristics Finish: White-Base, Blue OAP, Red Oxide Volume Solids: Weight Solids: For use over prepared steel or masonry surfaces in industrial and marine exposures such as: • Ballast tank interiors and oil storage tank interiors • Fuel storage tanks and external pipeline coating • Primary or Secondary containment • Acceptable for use with cathodic protection systems • Where rapid return to service and edge protection film build properties are required • Meets MIL-PRF-23236 Type VII, Class 5, 7, 5/18, 7/18, 13/18, 17, 17/18 Grade C requirements for single and multi-coat seawater, fuel, bilges, and CHT tanks • Blue OAP contains fluorescent pigment • Wind tower gearbox lining and transformer lining up to 204°F (96°C) • Suitable for use in the Mining & Minerals Industry Recommended Uses VOC (EPA method #24): <85 g/L; 0.71 lb/gal, mixed Mix Ratio: Recommended Spreading Rate per coat: Wet mils (microns) Dry mils (microns) ~Coverage sq ft/gal (m2/L) *Can be applied up to 60.0 mils (1500 microns) dft if required. Theoretical coverage sq ft/gal 1568 (38.4) (m2/L) @ 1 mil / 25 microns dft NOTE: Brush or roll application may require multiple coats to achieve maximum film thickness and uniformity of appearance. Drying Schedule @ 20.0 mils (500 microns): @ 40°F/4.5°C To touch: To handle: To recoat: minimum: maximum: Foot traffic: Cure to service: Pot Life: Sweat-in-Time: 6 hours 8-12 hours 6 hours 14 days 8-12 hours 36 hours Shelf Life: Flash Point: Reducer: Clean Up: Substrate*: Steel Surface Preparation*: SSPC-SP10 System Tested*: 1 ct. Fast Clad ER Epoxy @ 18.0-22.0 mils (450-550 microns) dft *unless otherwise noted below Test Name Performance Characteristics 1 hour 14 days 3 hours 24 hours 7 minutes None required 35 minutes 14 days 1 hour 12 hours 24 months Store indoors at 40°F (4.5°C) to 100°F (38°C) 230°F (110°C), PMCC, mixed Not recommended MEK (R6K10) or Reducer R7K104 Abrasion Resistance Adhesion Test Method ASTM D4060, CS17 wheel, 1000 cycles, 1 kg load ASTM D4541 Cathodic Disbondment Corrosion Weathering ASTM D5894, 4 cycles, 1134 hours Direct Impact Resistance Dry Heat Resistance Flexibility Results 22.4 mg loss >2000 psi Passes 30 days @ 1.5 volts (Cu/CuSO4), <10 mm disbondment radius Rating 10 per ASTM D610 for Rusting (field); Rating 10 per ASTM D714 for Blistering (field) 250°F (121°C) 7/16" (24-hour cure) Rating 10 per ASTM D610 for Rusting (field); Rating 10 per ASTM D714 for Blistering (field) H Moisture Condensation Resistance Pencil Hardness
Open the catalog to page 1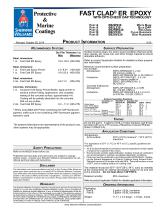
Fast Clad® ER Technology Epoxy With OPTI-Check OAP Protective & Marine Coatings Part A Part A Part A Part B Part B Product Information Recommended Systems Steel, immersion: 1 ct. Fast Clad ER Epoxy B62W230 White Base B62L230 Blue OAP B62RW230 Red Oxide B62V230 Clear Hardener B62AV230 Gray Hardener 9.50 Surface Preparation Dry Film Thickness / ct. Mils (Microns) Surface must be clean, dry, and in sound condition. Remove all oil, dust, grease, dirt, loose rust, and other foreign material to ensure adequate adhesion. Refer to product Application Bulletin for detailed surface preparation...
Open the catalog to page 2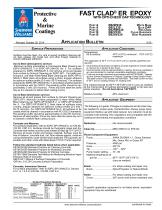
Fast Clad® ER Technology Epoxy With OPTI-Check OAP Protective & Marine Coatings Part A Part A Part A Part B Part B B62W230 White Base B62L230 Blue OAP B62RW230 Red Oxide B62V230 Clear Hardener B62AV230 Gray Hardener Application Bulletin Surface Preparations Surface must be clean, dry, and in sound condition. Remove all oil, dust, grease, dirt, loose rust, and other foreign material to ensure adequate adhesion. Iron & Steel (atmospheric service) Minimum surface preparation is Commercial Blast Cleaning per SSPC-SP6/NACE 3 or SSPC-SP12/NACE No. 5. For surfaces prepared by SSPC SP6/NACE 3,...
Open the catalog to page 3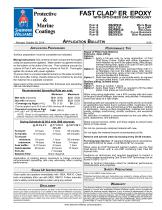
Fast Clad® ER Technology Epoxy With OPTI-Check OAP Protective & Marine Coatings Part A Part A Part A Part B Part B Application Bulletin Application Procedures Mixing Instructions: Mix contents of each component thoroughly using low speed power agitation. Make certain no pigment remains on the bottom or the sides of the can. Then combine one part by volume of Part A with one part by volume of Part B. Thoroughly agitate the mixture with power agitation. To ensure that no unmixed material remains on the sides or bottom of the cans after mixing, visually observe the container by pouring the...
Open the catalog to page 4All Sherwin-Williams catalogs and brochures
-
N51R301 / N51B301
4 Pages
-
TT-P-645C
4 Pages
-
TT-P-645B
4 Pages
-
TANKGUARD® EPOXY POLYAMIDE
4 Pages
-
SEAGUARD® 1000 MARINE ENAMEL
4 Pages
-
MIL-DTL-24441/19C TYPE III
4 Pages
-
FAST CLAD® BRUSH GRADE EPOXY
4 Pages
-
ANTI-GRAFFITI COATING
4 Pages
-
EURONAVY ES301L / ES301K
4 Pages
-
FAST CLAD® EPOXY PRIMER
4 Pages
-
SEAGUARD VOID COAT
2 Pages