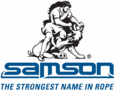
Catalog excerpts
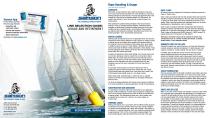
Rope Handling & Usage Use the Rope Properly When given a choice between ropes, select the strongest of any given size. A load of 200 pounds represents 2% of the strength of a rope with a breaking strength of 10,000 pounds. The same load represents 4% of the strength of a rope that has a breaking strength of 5,000 pounds. The weaker rope will have to work harder and as a result will have to be retired sooner. For the iPhone and iPad this handy app features: > Inspection and retirement criteria > Internal and external abrasion inspection information > Splice Instructions Download it at SamsonRope.com Line Selection Guide: Note carefully the quoted breaking strengths of the various Samson products. These are average breaking strengths. Published breaking strengths are determined by standard cordage testing and do not cover conditions such as sustained loads or shock loading. These strengths are attained under laboratory conditions. Remember also, that this is a breaking strength—not a recommended working load. Shock Loading Working loads as described herein are not applicable when rope has been subjected to shock loading. Whenever a load is picked up, stopped, moved, or swung there is an increased force caused by the dynamic nature of the movement. The force increases as these actions occur more rapidly or suddenly, which is known as “shock loading.” Synthetic fibers have a memory and retain the effects of being overloaded or shock loaded. A rope that has undergone shock loading can fail at a later time even though it is loaded within the working load range. Examples of applications where shock loading occurs include ropes used as a tow line, picking up a load on a slack line, or using rope to stop a falling object. In extreme cases, the force put on the rope may be two, three, or more times the normal load involved. Shock loading effects are greater on a low elongation rope such as polyester than on a high elongation rope such as nylon, and greater on a short rope than on a long one. For example, the shock load on a winch line that occurs when a 5,000 pound object is lifted vertically with a sudden jerk may “weigh” 30,000 pounds under the dynamic force. If the winch line is rated in the 30,000 pound break strength range, it is very likely to break. Where shock loads, sustained loads, or where life, limb, or valuable property is involved, it is recommended that an increased working load factor be used. For dynamic loading applications that involve severe exposure conditions, or for recommendations on special applications, consult the manufacturer. It is important to choose the right rope construction for your application because it affects resistance to normal wear and abrasion. Braided ropes have a round, smooth construction that tends to flatten out somewhat on a bearing surface. This distributes the wear over a much greater area, as opposed to the crowns of a 3-strand or, to a lesser degree, an 8-strand rope. 2090 Thornton Street Ferndale, WA 98248 USA Tel 01.360.384.4669 Fax 01.360.384.0572 SamsonRope.com © 2014 Samson Rope Technologies, Inc. All rights reserved. S/WD 108434 10K 08/2014 Working Loads Recreational marine Working load factors vary in accordance with the different safety practices and policies of each user. However, when used under normal conditions, our general recommendation that is fairly well accepted in the industry, is a minimum 5:1 working load factor. Thus, your maximum workload should be approximately 1/5th, or 20%, of the quoted breaking strength. This factor provides greater safety and extends the service life of the ropes. Rope Class All Samson ropes are categorized for splicing and testing purposes as a Class I or Class II ropes. Class I ropes are produced with non high-modulus fibers that impart the strength and stretch characteristics to the rope, which have tenacities of 15 grams per denier (gpd) or less and a total stretch at break of 6% or greater. Class I ropes are produced with traditional fibers such as olefins (polypropylene or polyethylene), nylon, or polyester. Class II ropes are produced with high-modulus fibers that impart the strength and stretch characteristics to the rope which have tenacities greater than 15 gpd and a total stretch at break of less than 6%. Typical ® Class II ropes are produced with HMPE (Dyneema ), HMPP (Innegra™-S), ® ® ® aramid (Technora ), LCP (Vectran ), or PBO (Zylon ). Both Class I and Class II ropes can be produced in various rope constructions such as 3-strand, 8-strand, 8x3-strand, 12-strand, double braids, or core-dependent braids. Minimize Twist in the Line A braided or plaited rope, being torque-free, can have twist induced by constant working on winches and capstans. If a twist develops, it can easily be removed by “counter-rotating” the rope when it is relaxed. In braided ropes, as little twist as four turns per three feet (or per meter) introduced into the line can cause as much as 10 to 30% reduction of strength. Another way to help prevent twist is to preset the line. Once these ropes have been loaded, they do not return to their original dimensions. A rope that has been preset is less likely to accept permanent twist. Presetting should be performed only on new and unused rope, and with extreme caution. For lines in use that have not been preset, alternate wrap directions on the bitt to minimize twist each time the line is used Avoid Overheating Heat can seriously affect the strength of synthetic ropes. When using rope where the temperature exceeds 250° (or if it is too hot to hold), consult the manufacturer for recommendations as to the size and type of rope for the proposed continuous heat-exposure conditions. When using ropes on a capstan or winch, care should be exercised to avoid surging while the capstan or winch head is rotating. The friction from the slippage causes localized overheating, which can melt or fuse synthetic fibers, resulting in severe loss of tensile strength. While it is true that a knot reduces rope strength, it is also true that a knot is a convenient way to accomplish rope attachment. The strength loss is a result of the tight bends that occur in the knot. With some knots, ropes can lose approximately 50% of their strength. However, this number can be higher or lower based on rope construction and fibers used. It is vital that the reduction in strength by the use of knots be taken into account when determining the size and strength of a rope to be used in an application. To avoid knot strength reduction, it is recommended that a rope be spliced according to the manufacturer’s instructions. Splice terminations are used in all our ropes to determine new and unused tensile strengths. Therefore, whenever possible, spliced terminations should be used to maximize the rope strength for new and used ropes.
Open the catalog to page 1All Samson catalogs and brochures
-
Offshore Sling Brochure
6 Pages
-
Vessel Mooring System
20 Pages
-
Chafe Gear Brochure
12 Pages
-
Saturn-12 Brochure
4 Pages
-
AGILE™ Lifting System
8 Pages
-
The Ultimate Towing System
24 Pages
-
Recreational Marine Catalog
38 Pages
-
Tug Brochure
8 Pages
-
Mooring Brochure
4 Pages
-
AmSteel-Blue
2 Pages
-
Recreational Running Rigging
38 Pages
-
Commercial Marine
88 Pages