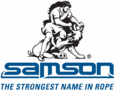
Catalog excerpts
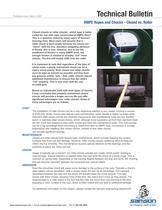
Published date: March, 2007 Technical Bulletin HMPE Ropes and Chocks - Closed vs. Roller Closed chocks or roller chocks - which type is better suited for use with rope constructed of HMPE fiber? This is a question asked by many users of Samson mooring lines. Most users will assume that a roller chock is best simply because the chock can "move" with the line, therefore mitigating abrasion. In theory, this is true. However, due to the low coefficient of friction in many HMPE lines, not enough friction is created to actually "roll" most chocks. The line will simply slide over the roller. It is important to note that regardless of the type of chock used, a poorly maintained chock can be a rope's worst enemy. Both closed and roller chocks must be kept as smooth as possible and free from any grooves and/or "pits." And, roller chocks require additional maintenance to ensure that the rollers "roll" properly. This is true even with the use Based on substantial trials with both types of chocks, it was concluded that properly maintained closed chocks will provide a longer service life and offer significant advantages over roller chocks. Some of these advantages are as follows: The installation of roller chocks can be a very expensive addition to any vessel, running in excess of $100,000. Roller chocks also require more maintenance, which results in higher up-keep costs. Standard steel closed chocks are relatively inexpensive, and maintenance costs are low. Another option is stainless steel closed chocks, which, although more expensive up front than standard steel, are still much less expensive than roller chocks and have low maintenance costs. This cost savings can be a big advantage when converting a vessel from wire to HMPE rope. Conversion is a costly expenditure and installing new closed chocks, instead of new roller chocks, can provide significant savings. Closed and roller chocks both require basic maintenance, which includes keeping the contact surfaces free from rust and damage. However, roller chocks require additional effort to keep the rollers moving smoothly. This maintenance requires special attention to the bearings, and the positions at which the rollers are set. Usage is typically not a concern, but roller chocks actually can create "pinch points" leading to rope damage. Special attention is needed when the rope exits the chock at a sharp angle. This is common on spring lines. Depending on the varying heights between the ship and berth, the mooring line can become "jammed" between the horizontal and vertical rollers. Even the smoothest chock will cause some damage to the surface of the rope. Typically a chock's wear pattern will be consistent - with a closed chock this can be an advantage. The constant movement between the rope and the chock will actually keep the chock smooth. This also occurs with roller chocks, because most of the time, the rollers don't move as they should. The disadvantage to a roller chock is the fact that the roller will move from one mooring to the next, exposing a "new" surface to the rope, which is often rusted and can lead to additional damage. For additional information on this subject, please contact the Samson engineering department. www.samsonrope.com | Email custserv@samsonrope.com | Tel +1.360.384.4669 THE STRONGEST NAME IN ROPE
Open the catalog to page 1All Samson catalogs and brochures
-
Offshore Sling Brochure
6 Pages
-
Vessel Mooring System
20 Pages
-
Chafe Gear Brochure
12 Pages
-
Saturn-12 Brochure
4 Pages
-
AGILE™ Lifting System
8 Pages
-
The Ultimate Towing System
24 Pages
-
Recreational Marine Catalog
38 Pages
-
Tug Brochure
8 Pages
-
Mooring Brochure
4 Pages
-
AmSteel-Blue
2 Pages
-
Recreational Running Rigging
38 Pages
-
Commercial Marine
88 Pages