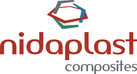
Group: Nidaplast
Catalog excerpts

What is the nidaplast® honeycomb ? nidaplast® advantages Lamination range Bonding range Our Fire and High-Performance products Our reinforced honeycomb structures General recommendations Tailor-made panels Nidaplast services
Open the catalog to page 3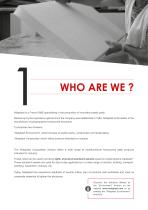
Nidaplast is a French SME specialising in the production of innovative plastic parts. Backed up by the experience gained since the company was established in 1984, Nidaplast is the leader in the manufacture of polypropylene honeycomb structures. It comprises two divisions: ‘Nidaplast Environment’, which focuses on public works, construction and landscaping. ‘Nidaplast Composites’ which offers products intended for industry. The ‘Nidaplast Composites’ division offers a wide range of multifunctional honeycomb core products intended for industry. These cores can be used to produce light,...
Open the catalog to page 4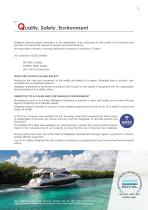
Quality, Safety, Environment Nidaplast attaches great importance to the satisfaction of its customers by the quality of its products and services, but also to the respect for people and its environment. We have been involved in a strong certification process for more than 15 years. Our company is QSE certified: ISO 9001 Quality, OHSAS 18001 Safety, ISO 14001 Environment. INVOLVED IN HEALTH AND SAFETY Abiding by the rules and concerned for the health and safety of its teams, Nidaplast aims to achieve ‘zero accidents and occupational illnesses’. Nidaplast implements a prevention procedure...
Open the catalog to page 5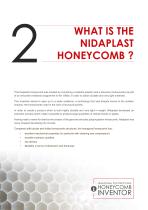
WHAT IS THE NIDAPLAST HONEYCOMB ? Thermoplastic honeycomb was created by combining a material (plastic) and a structure (honeycomb) as part of an innovative research programme in the 1980s, in order to obtain durable and very light materials. This invention aimed to open up to a wider audience, a technology that was already known in the aviation industry: the honeycombs used in the core of structural panels. In order to create a product which is both highly durable and very light in weight, Nidaplast developed an extrusion process which made it possible to produce large quantities of...
Open the catalog to page 6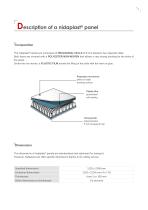
Composition The nidaplast® panels are composed of HEXAGONAL CELLS of 8 mm between two opposite sides. Both faces are covered with a POLYESTER NON-WOVEN that allows a very strong bonding for the skins of the panel. Under the non woven, a PLASTIC FILM avoids the filling of the cells with the resin or glue. Polyester non-woven offers an ideal bonding surface Plastic film guaranteed cell sealing Honeycomb polypropylene 8 mm hexagonal cell Dimensions The dimensions of nidaplast® panels are standardized and optimized for transport. However, Nidaplast can offer specific dimensions thanks to its...
Open the catalog to page 7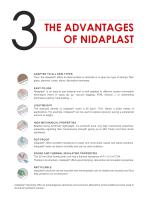
ADAPTED TO ALL SKIN TYPES Thus, the nidaplast® offers an ideal surface to laminate or to glue any type of facings: fiber glass, plywood, metal, stone, decorative laminates... EASY-TO-USE Nidaplast® is an easy-to-use material and is well adapted to different modern lamination techniques (hand or spray lay up, vacuum bagging, RTM, infusion…) or assembling techniques (gluing, heat-sealing…) LIGHTWEIGHT The standard density of nidaplast® cores is 65 kg/m3. This allows a wider variety of applications. For example, nidaplast® can be used to replace plywood, saving a substantial amount of weight....
Open the catalog to page 8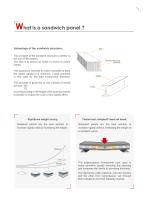
What is a sandwich panel ? Advantage of the sandwich structure: The principle of the sandwich structure is similar to the use of IPN beams. The idea is to space out ‘sides’ or ‘skins’ to create inertia. Honeycomb core material This spacing is intended to make it possible to keep the added weight to a minimum, a goal achieved in this case by the light honeycomb structure. This principle is governed by the moment of inertia formula: bh3 12 h (corresponding to the height of the spacing) makes it possible to impact the cube of this rigidity effect. Significant weight saving Flexion test:...
Open the catalog to page 9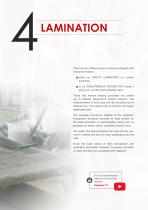
There are two different ways of working nidaplast® with manual lamination: either by DIRECT LAMINATION (or contact moulding) or by SIMULTANEOUS PROJECTION (using a spray gun, cut fibre and catalysed resin) These fully manual shaping processes are carried out at ambient temperature without pressure. The implementation is fairly easy and the moulding cost is relatively low. This method can be used for very large, lightweight parts. The polyester non-woven material on the nidaplast® honeycomb structures provides an ideal surface for the direct lamination of thermosetting resins such as...
Open the catalog to page 10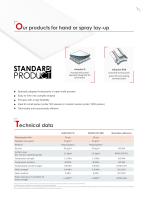
Our products for hand or spray lay-up nidaplast 8 Honeycomb panel specially designed for lamination nidaplast 8DB Grooved honeycomb panel for laminating rounded parts Specially adapted honeycomb to open-mold process Easy to form into complex shapes Process with a high flexibility Ideal for small series (under 500 pieces) or medium series (under 1000 pieces) Technically and economicaly efficient Technical data NIDAPLAST 8 Polypropylene film Polyester non-woven Normative references Surfacic mass (for a 20 mm sandwich panel) Compressive strength Compressive modulus Perpendicular tensile...
Open the catalog to page 11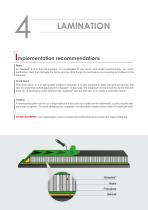
Implementation recommendations Resin As nidaplast® 8 is a thermal insulator, it is preferable to use resins with limited exothermicity. An overly exothermic resin may damage the skins, among other things by overheating and creating air bubbles in the laminate. Thick skins With thick skins, or if a high-quality surface is required, it is also possible to allow the gelcoat and the first skin to polymerise before applying the nidaplast®. In this case, the nidaplast® will be rebonded to the first skin either by re-laminating a mat between the nidaplast® and the first skin or by using a...
Open the catalog to page 12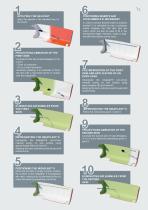
Apply the gelcoat in the standard way on the mould. POSITIONING INSERTS AND ATTACHMENTS IF NECESSARY In order to ensure that the insert is properly bonded, it is advisable to use a polyester mastic between the first skin and the insert, which will also be used to fill in the honeycomb edges. Wooden, metal or highdensity foam inserts can be used. PROJECTION/LAMINATION OF THE FIRST SKIN Laminate the first skin of resin-fibreglass (1.5 to 2 mm): - Either by projection - Or by contact lamination Generally speaking, it is preferable to finish this skin with a mat which will be in contact with...
Open the catalog to page 13All Nidaplast catalogs and brochures
-
brochure nautisme
2 Pages