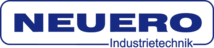

Catalog excerpts
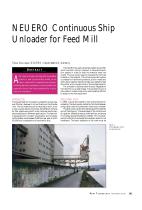
NEUERO Continuous Ship Unloader for Feed Mill T OMAS K ISSLINGER , NEUERO Industrietechnik, Germany ABSTRACT fter close to 50 years working with an unloading system, a new system which would serve today’s needs and be compatible was planned. Flexibility, operation, maintenance, the environment and especially the cost had to be considered for a quick return of investment. The Feed Mill has used a pneumatic system since 1938, which was still running. However, it required three to four people in order to help the material enter the nozzle. This was not an easy job, because the men had to stand on the material. The normal pneumatic system is suitable for free-flowing material, but for meals and other damp material mechanical help was needed to feed the nozzle, which caused a drop in the average capacity. The unloader is stationary and directly integrated to the Feed Mill via a steel bridge. The old steel structure was made of riveted construction and therefore difficult to adapt to the new equipment. PRELIMINARY STUDY The Garant feed mill is located in a beautiful tourist area, near Pöchlarn between Linz and Vienna on the Danube river. The raw materials can be received by train, truck or ship. Garant delivers more than 250 different mixtures for their clients every month. Each client also has his own secret additives for different applications. The feed mill is equipped with a modern visualisation and computer control system and processes 35,000 tons per year, of which 30,000 tons is expected to be received by ship. In 1994, a study was started to look at alternatives for unloading. The study quickly centred on the choice between using a grab crane or a pneumatic continuous unloader. The grab crane was the first idea because the materials are not free-flowing. The advantages of the multiple use of a grab for different products, even fertilizer, are strong if a multipurpose discharging is needed. This, however, was not sufficient to outweigh the necessary space for the installation. The batch operation of the crane must be Figure 1 Old installation of the Garant feed mill
Open the catalog to page 1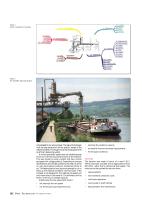
Figure 2 Factors considered in the study Figure 3 The NEUERO stationary flexiport compensated for by using a hopper. The grab and the hopper must be large because of the low specific weight of the material handled. This hopper must also be equipped with an efficient dedusting system. A normal pneumatic system was not suitable because of the non free-flowing characteristics of the material. This was solved by using a system that has a nozzle equipped with a digging device. Depending on process characteristics and climate conditions, the meal can arrive in a very hard packed condition,...
Open the catalog to page 2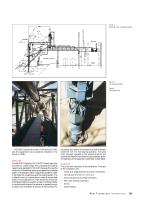
Figure 4 Drawing of the complete Flexiport Figure 5 The bridge structure Figure 6 The rotating hoe NEUERO received the order in the spring of 1998, and the equipment was successfully installed in the winter of 1998. unloading, the material is conveyed to a bucket elevator inside the mill. For the loading operation, the same chain conveyor operates in the reverse direction and receives the material from another bucket elevator spout. The operation of the equipment is described in detail below. OPERATION The NEUERO Stationary FLEXIPORT stands vertically mounted on a steel bridge. The...
Open the catalog to page 3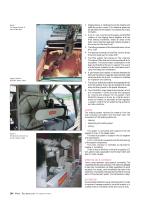
Figure 7 The digger reaches all areas of the hatch 1. Digging device. A rotating hoe cuts the material and feeds the suction nozzle. The rotational speed can be adjusted and the system is protected by torque limitation. 2. Kick in / kick out at the vertical pipe, and the 360º rotation of the digging device together with the filter slewing movement, means all areas of the hatch can be reached, especially material located in the corners of the ship’s hold. 3. The luffing movement of the horizontal boom is from 0º to +55º. 4. The slewing movement of the filter column allows the entire upper...
Open the catalog to page 4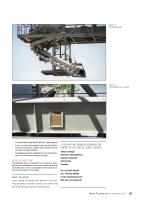
Figure 10 The loading system Figure 11 The reversible chain conveyor The sound level is less than 85 dBA at 1 metre distance. Dust is virtually eliminated by the use of the filter. There is no product contamination because of the enclosed conveying system. The appearance of the installation is not a visual intrusion into the attractiveness of the area. IF YOU HAVE ANY ENQUIRIES REGARDING THE CONTENT OF THIS ARTICLE , PLEASE CONTACT: Tomas Kisslinger NEUERO Industrietechnik Buersche Strasse 60 RETURN ON INVESTMENT The expected return of investment is in less then 5 years, taking into...
Open the catalog to page 5All NEUERO Industrietechnik GmbH catalogs and brochures
-
SHIP LOADER 600t/h
1 Pages
-
SHIP LOADER 800 t/h
1 Pages
-
TWO SHIP LOADERS
1 Pages
-
Grain Ship Loader
1 Pages
-
SL500DNS–500t/h S
1 Pages
-
AW-Ship-Unloader-Design
2 Pages
-
Shipunloader Multiport M400
1 Pages
-
Stationary M300
1 Pages
-
Multiport M600
1 Pages
-
Multiport M400 for Alumina
1 Pages
-
The Netherlands 2003
1 Pages
-
Multiport M400
1 Pages
-
MULTIPORT GF GS 300 t/h
1 Pages
-
Multiport M300
2 Pages
Archived catalogs
-
SHIP LOADER : 500 t/h
1 Pages
-
SHIP LOADERS 180 tph grain
1 Pages
-
tower
1 Pages
-
MULTIPORT on rails
1 Pages
-
STATIONARY SHIPUNLOADER
1 Pages