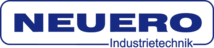

Catalog excerpts
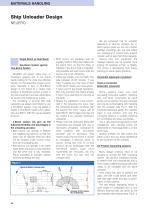
MATERIALS HANDLING Ship Unloader Design NEUERO Single Boom vs Dual Boom Two-Boom System against One-Boom System NEUERO will design either One- or Two-Boom systems acc. to our clients needs looking for the most cost effective solution for the respective project conditions. Basically, a Two- or One-Boom design is not linked to a certain bulk material. A One-Boom system is lower in the total investment, and also expenditure for service and maintenance is less. For unloading of alumina with high capacities we always recommend to use a Two-Boom system. If we are asked to supply a One-Boom system (for capacities up to 800 or 1000 t/h), we are capable to do so. 2-Boom system will give us the following flexibility and advantages in the unloading process: • Both booms can operate in different but neighbouring hatches, so that one hatch can be cleaned while the other will be emptied under normal conditions at full unloading rate. • Both booms can operate in the same hatch while one boom is fully extended and the other one is fully retracted. Equal unloading is possible without trimming (levelling) the ship. Figure 1: • Both booms are equipped with an auxiliary hoist for lifting pay loaders into the ship’s hold, so that the lifting of bobcats in the ship’s hold is independently possible with each boom while the second one is still unloading. • Lifting pay loaders into the hatch may take between 20-30 minutes. If you have 7 hatches you may have at least 10 lifts which means you loose approx. 5 hours just for pay loader operations. With only one boom that means at least 5 hours more downtime for the ship at the berth. • Should any breakdown of any component in the conveying line occur, then the unloading process continues with the second line which means with at least 400 t/h. Demurrage costs may not be a factor if you maintain continuous unloading. • Please note that Horizontal Telescopic movements are possible with one or Two-boom unloaders, compared to other systems with One-boom unloader with no telescopic. That means every time the boom is moved its throughput is reduced, since, of course, during that time no or less product can be discharged. With the One-Boom system much more movements are necessary not only with the boom but also with the unloader itself. We are convinced that for unloader operations at alumina smelters the 2boom version gives you not only a higher average unloading rate, but also keeps you operational in almost every present situation with at least half of the capacity. Having only one equipment the average capacity can be reduced more looking the example at Plan vs Reality. This shows a discrepancy from theory planning to actual reality operation. Horizontal telescopic movement Fixed vs horizontal telescopic movement Some systems have one fixed conveying horizontal system; therefore only with polar movements all hatch points can be reached. The area coverage can only be compensating with travelling with the unloader (see Fig.1). With the horizontal telescopic ability, the unloader stays in one position, and only the conveying distance is variable, therefore X-Y coordinates and polar coordinates. This is very important especially in fixed installations, were docking points are determined or more equipment is on the same quay. Another problem are ship cranes and hatch covers that can bring interference to the movement of the unloader. Air-Product separating systems Many design criteria’s need to be decided to choose the right unloading system. The alumina unloading industry is different with one characteristic that in many cases a different product (pet coke) needs to be unloaded with the same unloader. Here mainly two type of systems are used, one with a belt airlock and other with slide gate valves and also a combination of both systems. The belt airlock separating device is quite simple to understand and is very efficient. External belts are driven by the rotor therefore with reduce
Open the catalog to page 1
MATERIALS HANDLING problem increases with the size of the unloading equipment. By dual boom unloader systems at least power consumption can be saved at least by 50% switching off the power of one line during the clean-up operation. Simulation Standard airlocks with adjustable tips were used in the past, but were too expensive and required too much maintenance. The slide gate valve system requires a product column to separate the ambient from the vacuum in the filter. This requires level indicators and additional height. Plan vs Reality The drive features adjustable speed using a frequency...
Open the catalog to page 2All NEUERO Industrietechnik GmbH catalogs and brochures
-
SHIP LOADER 600t/h
1 Pages
-
SHIP LOADER 800 t/h
1 Pages
-
TWO SHIP LOADERS
1 Pages
-
Grain Ship Loader
1 Pages
-
SL500DNS–500t/h S
1 Pages
-
Shipunloader Multiport M400
1 Pages
-
Stationary M300
1 Pages
-
Multiport M600
1 Pages
-
Multiport M400 for Alumina
1 Pages
-
The Netherlands 2003
1 Pages
-
Multiport M400
1 Pages
-
MULTIPORT GF GS 300 t/h
1 Pages
-
Multiport M300
2 Pages
Archived catalogs
-
SHIP LOADER : 500 t/h
1 Pages
-
SHIP LOADERS 180 tph grain
1 Pages
-
tower
1 Pages
-
MULTIPORT on rails
1 Pages
-
STATIONARY SHIPUNLOADER
1 Pages