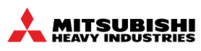

Catalog excerpts
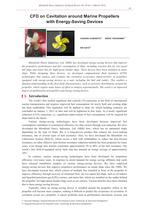
Mitsubishi Heavy Industries Technical Review Vol. 49 No. 1 (March 2012) 63 CFD on Cavitation around Marine Propellers with Energy-Saving Devices CHIHARU KAWAKITA*1 REIKO TAKASHIMA*2 KEI SATO*2 Mitsubishi Heavy Industries, Ltd. (MHI) has developed energy-saving devices that improve the propulsive performance and fuel consumption of ships, including reaction fins for low-speed full ships and stator fins for high-speed slender ships. These devices have been installed on many ships. While designing these devices, we developed computational fluid dynamics (CFD) technologies that analyze and evaluate the cavitation occurrence characteristics of propellers equipped with energy-saving devices as a unit, including the hull and rudder. This enables a detailed understanding of the flow-field characteristics, such as pressure distributions around the propeller, which require many hours of effort to analyze experimentally. The result is an improved degree of optimization of propellers and energy-saving devices. |1. Introduction The world’s first unified regulation that controls CO2 emissions in the field of international marine transportation and requires improved fuel consumption for newly built and existing ships has been established. This regulation will be applied to ships for which building contracts are concluded on January 1, 2013 or later and will be tightened in four steps. As a result, significant reduction of CO2 emissions, i.e., significant improvement of fuel consumption, will be required for ships built in the future. Various energy-saving technologies have been developed because improved fuel consumption contributes to economical efficiency for ship owners through cost reduction. We have developed the Mitsubishi Heavy Industries, Ltd. (MHI) bow, which has an optimized shape depending on the type of ships; this is a long-proven product that reduces the wave-making resistance, one of several types of hull resistance. Also, we have developed the Mitsubishi Air Lubrication System (MALS), which covers a hull with millibubbles to reduce the skin-friction resistance; no other effective skin-friction resistance reduction method has been proposed for many years, even though skin friction constitutes approximately 50 to 80% of the hull resistance. The world’s first MALS-equipped newly built ship has attained an energy savings of approximately 10%.1 In contrast, various energy-saving technologies have been developed for propulsion efficiency over many years. In response to recent demand for energy saving, different ship yards have released installation samples of various energy-saving devices. We have employed energy-saving devices that improve propulsive performance on actual ships since the 1980s. We have developed reaction fins, which consist of multiple fins installed in front of the propeller to improve efficiency through recovery of rotational flow, for low-speed full ships, such as oil tankers and liquefied petroleum gas (LPG) carriers, and stator fins, which are installed on the rudder behind the propeller, for high-speed slender ships such as car carriers. Various benefits have been obtained due to these energy-saving devices. Typically, when an energy-saving device is installed around the propeller, inflow to the propeller will become more complex, making it difficult to predict the occurrence of cavitation. If cavitation occurs on a propeller, it causes problems such as performance decrement, erosion, and *1 Research Manager, Nagasaki Research & Development Center, Technology & Innovation Headquarters *2 Nagasaki Research & Development Center, Technology & Innovation Headquarters
Open the catalog to page 1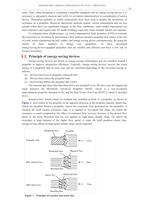
Mitsubishi Heavy Industries Technical Review Vol. 49 No. 1 (March 2012) 64 noise. Thus, when designing or evaluating a propeller equipped with an energy-saving device, it is necessary to adequately examine and verify its cavitation characteristics in consideration of such a device. Theoretical methods or model experiments have been used to predict the occurrence of cavitation on a propeller. However, theoretical methods require various assumptions and are less reliable when there are significant changes in the flow conditions, while model experiments are more expensive and require time for...
Open the catalog to page 2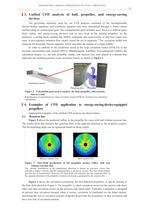
Mitsubishi Heavy Industries Technical Review Vol. 49 No. 1 (March 2012) 65 |3. Unified CFD analysis of hull, propeller, and energy-saving devices The governing equations used for our CFD analyses consisted of the incompressible Navier–Stokes equations and continuity equation and were discretized through a finite-volume method using an unstructured grid. The computational grid included areas fixed to a defined space (hull, rudder, and energy-saving devices) and an area fixed to the rotating propeller. At the junctions, a sliding mesh method that fulfills continuity and conservation of...
Open the catalog to page 3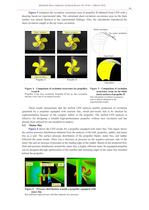
Mitsubishi Heavy Industries Technical Review Vol. 49 No. 1 (March 2012) 66 Figure 5 compares the cavitation occurrence area of propeller B obtained from CFD with a drawing based on experimental data. The calculated sheet cavitation occurrence area on the back surface was almost identical to the experimental findings. Also, the calculations reproduced the sheet cavitation caught in the tip vortex cavitation. Figure 4 Comparison of cavitation occurrence for propellers A and B Propeller A has face cavitation. Propeller B has no face cavitation and has a low risk of cavitation erosion. Figure 5...
Open the catalog to page 4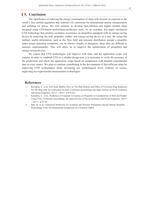
Mitsubishi Heavy Industries Technical Review Vol. 49 No. 1 (March 2012) 67 |5. Conclusion The significance of reducing the energy consumption of ships will increase in response to the world’s first unified regulation that controls CO2 emissions for international marine transportation and inflating oil prices. We will continue to develop fuel-efficient and highly reliable ships designed using CFD-based performance-prediction tools. As an example, this paper introduced CFD technology that predicts cavitation occurrence on propellers equipped with an energy-saving device by analyzing the hull,...
Open the catalog to page 5All MITSUBISHI HEAVY INDUSTRIES - Ship & Ocean catalogs and brochures
-
Product Profile
6 Pages
-
MHI GUIDE BOOK 2011
156 Pages
-
The 155k-m3 Sayaendo
6 Pages
-
MET TURBOCHARGER
4 Pages
-
BOILER : MAC-B
14 Pages
Archived catalogs
-
Auxiliary Boiler MAC-B
14 Pages
-
Steam Turbine Generator
55 Pages