
Catalog excerpts
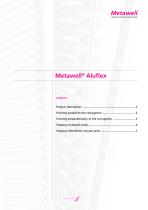
metal sandwich technology Metawell® Aluflex Metawell® Aluflex
Open the catalog to page 1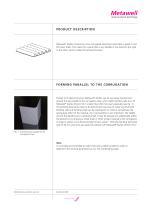
metal sandwich technology
Open the catalog to page 2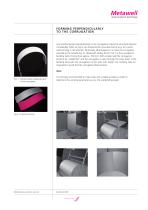
metal sandwich technology For m ing p er p endi cularly t o th e corrugation Any transformation perpendicularly to the corrugation makes the structural element considerably stiffer so that it can frequently be mounted directly (e.g. for curved ceiling linings in rail vehicles). Particularly advantageous is to have the corrugation exposed to the outside (fig. 2). Metawell® Aluflex 05-02 / H4.7 is thus suitable for bending radii of more than approx. 100 mm. With smaller radii the corrugation tends to be „pulled flat“ and the corrugation is seen through the cover sheet. Is the bending done...
Open the catalog to page 3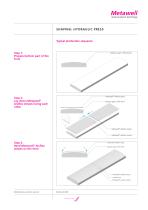
metal sandwich technology Typical production sequence Step 1: Prepare bottom part of the form bottom part of the form Metawell® Aluflex stripe Step 2: Lay down Metawell® Aluflex stripes facing each other bottom part of the form Metawell® Aluflex stripe 1 Metawell® Aluflex stripe 2 Step 3: Bend Metawell® Aluflex stripes on the form Metawell® Aluflex stripe bottom part of the form Metawell® Aluflex stripe 1 contact line Metawell® Aluflex stripe 2 Modifications and errors reserved
Open the catalog to page 4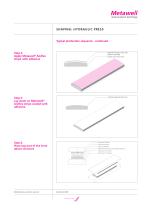
metal sandwich technology Typical production sequence - continued Step 4: Apply Metawell® Aluflex stripe with adhesive Metawell® Aluflex stripe with adhesive (bended) bottom part of the form bottom part of the form Step 5: Lay sheet on Metawell® Aluflex stripe coated with adhesive Step 6: Place top part of the form above structure top part of the press top part of the form sheet (not bended) Metawell® Aluflex stripe with adhesive (bended) bottom part of the form bottom part of the press Modifications and errors reserved Metawell® Alufl
Open the catalog to page 5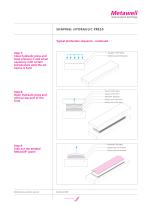
metal sandwich technology Typical production sequence - continued Step 7: Close hydraulic press and keep pressure if and when necessary with certain temperature until the adhesive is hard top part of the press bottom part of the press Step 8: Open hydraulic press and remove top part of the form top part of the form Metawell® (bended) bottom part of the form bottom part of the press Metawell® (bended) Step 9: Take out the bended Metawell® panel Modifications and errors reserved bottom part of the form bottom part of the press Metawell® Alufle
Open the catalog to page 6
metal sandwich technology Typical production sequence - continued Step 4: Apply Metawell® Aluflex stripe with adhesive Metawell® Aluflex stripe with adhesive (bended) bottom part of the form Step 5: Lay sheet on Metawell® Aluflex stripe coated with adhesive Metawell® Aluflex stripe with adhesive (bended) bottom part of the form Step 6: Place membrane of the press above structure top part of the press membrane sheet (not bended) Metawell® Aluflex stripe with adhesive (bended) bottom part of the form bottom part of the press Modifications and errors reserved Metawell® Aluf
Open the catalog to page 8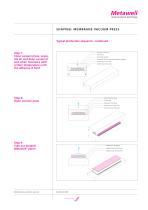
metal sandwich technology Typical production sequence - continued Step 7: Close vacuum press, evacuate air and keep vacuum if and when necessary with certain temperature until the adhesive is hard top part of the press membrane sheet (not bended) Metawell® Aluflex stripe with adhesive (bended) bottom part of the form bottom part of the press Step 8: Open vacuum press top part of the press membrane Metawell® (bended) bottom part of the form bottom part of the press Step 9: Take out bended Metawell® panel Modifications and errors reserved Metawell® (bended) bottom part of the form bottom part...
Open the catalog to page 9All Metawell GmbH- metal sandwich technology catalogs and brochures
-
Metawell® data sheets
11 Pages
-
Aluflex hl 08-03 hl / H9,8*
1 Pages
-
Aluflex hl 05-02 hl / H4,7
1 Pages