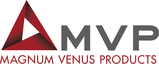

Catalog excerpts
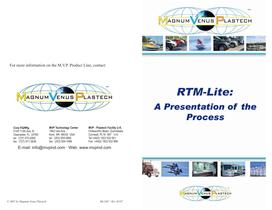
For more information on the M. VP. Product Line, contact: Corp HQ/Mfg. MVP Technology Center MVP - Plastech Facility U.K. 5148 113th Ave. N. 1862 Ives Ave. Chilsworthy Beam, Gunnislake Clearwater, FL 33760 Kent, WA 98032 USA Cornwall, PL18 9AT ■ U.K. E-mail: info@mvpind.com ■ Web: www.mvpind.com © 2007 by Magnum Venus Plastech.
Open the catalog to page 1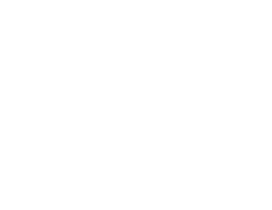
The Technical Flange of the Mold 3 Dimensions of the Technical Flange 6 Building of the Technical Flange 7
Open the catalog to page 3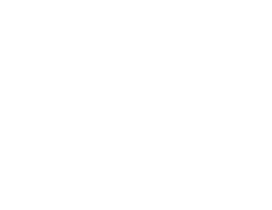
RTM-Lite is a vacuum assisted RTM (Resin Transfer Molding) system with a low pressure resin injection system (lower than 1 Two levels of vacuum are needed: higher, is used to close the molds. is used to facilitate the resin flow during injection. With low pressure RTM Lite, the molds need not be sophisticated and are relatively easy and quick to build. The counter mold is semi-rigid and is low weight which makes it
Open the catalog to page 4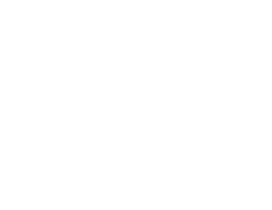
Shown below are accessories, specially designed for the RTM Lite System. They are more efficient and easier to clean after use. Vacuum bowl insert Gasket Material Gasket Material Vacuum Bowl Resin excess retrieval Gasket Material Foam Outer/ Silicone Mold Silicone Rubber Mold Rubber Channel Foam Rubber Inner Seal Seal Pattern Mold Seal -1/4" dia. The simplicity of the system means that it is possible to start production without a major investment. The mold is a simple construction. The Gelcoat and the resins used should have an HDT of at For best results, the air gap should be made with...
Open the catalog to page 5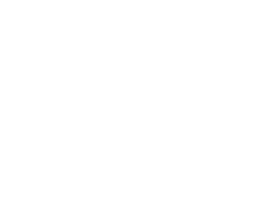
The closure and tightness of the mold is achieved with seals that are glued to the injector/vacuum ramp on the counter mold. A vacuum channel is created on either the positive or negative mold. On either side of the vacuum channel is an inner and outer seal (silicone inner seal and wind outer seal) The internal seal provides excellent vacuum tightness and the inner seal prevents the resin from flowing into the vacuum cavity at the time of injection. It is critical that the inner seal is maintained and that the mold seals properly - not only to keep the resin from penetrating into the vacuum...
Open the catalog to page 6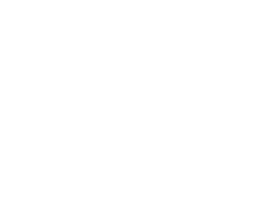
Accessories: Vacuum Assist The vacuum assist bowl lid is used to seal the top of the bowl and allow for the vacuum assist line to be connected to the top. The vacuum assist bowl and lid act as a separator preventing any resin from being sucked into the vacuum line or vacuum pump. Normally the bowl lid is made of a transparent material, like Acrylic or glass so inside of the bowl can be observed as the resin begins to enter. If the bowl and lid are used in conjunction with a resin meter or fed by a transparent poly tube the lid could be made of any material that could be fitted with fittings...
Open the catalog to page 7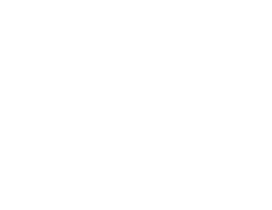
The edges of the mold are horizontal and 6 inches wide (15.24 cm) wide. It is therefore easy to transform an existing mold into an injection mold; it is only necessary to add horizontal panels. The mold is stiffened with a sandwich core, which will prevent any deformations during injection. It is the thinner counter mold which may deform (being only 0.156 inches - 0.39 cm - thick). The sandwich also retains the heat created by the polymerization of the first part. This will also help to accelerate the polymerization of the Gelcoat on following part and thus, reduce cycle time. Accessories:...
Open the catalog to page 8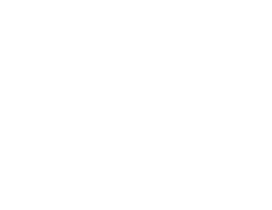
Accessories: Vacuum Assist The vacuum assist bowl and lid act as a separator preventing any resin form being drawn into the vacuum line or vacuum pump. There are many solutions that can be employed to accomplish what the vacuum assist bowl / separator bowl is doing. Many of these can be constructed using inexpensive readily available materials. One of the best solutions is to purchase an inexpensive stainless steel or suitable plastic bowl from a local source, approximately 1-3 quarts (1-3 liters), in conjunction with a simple to make lid (see Vacuum Assist Bowl Lid). The bowl should be...
Open the catalog to page 9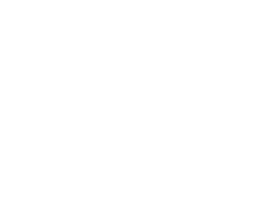
Building the Technical Flange It is best to create the injector/vacuum area (the Technical Flange) yourself, directly on the mold, in order to adapt it to the shape of the ramps which are not always straight and flat. A rectangular silicone seal is used, as it is very easy to fit with contact adhesive. The core of the central area is made of foam (preferably PVC) which may be shaped rapidly and covers the PVC tape. For the air-seal, three successive layers of 1/8 inches (3mm) wax are Do not forget to use clay (plastline) to round off internal protruding The injector is placed at the edge of...
Open the catalog to page 10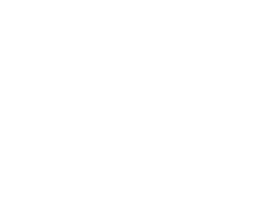
This pot, which is placed at the center of the mold, receives excess resin. (This is not supplied by MVP.) It is composed of three parts: • a metal sleeve which is installed when the counter mold is The cover sealing gasket is made of Neoprene; its %" (19mm) base allowing good adhesion. The cover is made of normal ± %" laminate, with a possible location for plexiglass or glass depending on current safety rules. Vacuum Assisi Vacuum Assist Bowl Lid Vacuum Assist Bowl There is a way to reduce the time needed to construct the counter mold: using a profile. If the edges of the original mold are...
Open the catalog to page 11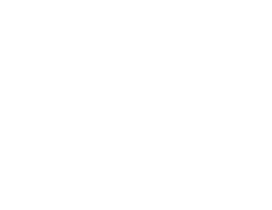
If the contour of the mold, after the profile is positioned, is curved rather than straight, the profile should be laminated oversize and After cutting and fitting the angles, the pieces of the profile are laminated together. Then, after beveling the edges, the assembly is clamped on to the mold, with the air gap formed by calibrated The counter mold is then laminated onto the section with an overlap The injector (RTM-3000) is used for the RTM-Lite application. A small PE or PA 25/64" (10 mm) tube is placed in position at the time of the injection; it will not need to be drilled out after...
Open the catalog to page 12All Magnum Venus Products catalogs and brochures
-
Patriot Innovator
1 Pages
-
Patriot Multi-Color
1 Pages
-
PRO RIDER
1 Pages
-
UltraMax Multi-Color
1 Pages
-
ULTRAMAX™
1 Pages
-
MINI-PRO CHOP/WETOUTSYSTEM
1 Pages
-
Precision Gelcoat Unit
2 Pages
-
Single-Component UNIT
2 Pages
-
Gold Line - Accessories
3 Pages
-
Cartridge Filling Station
2 Pages
-
MVP White Line - Epoxy
2 Pages
-
MVP Silver Line - Guns
1 Pages
-
MVP Red Line - Adhesives
3 Pages
-
MVP Green Line - Closed Mold
2 Pages
-
MVP Blue Line - Gelcoat
2 Pages
-
Micro Pro
2 Pages
-
DURAMAX GUN
2 Pages
-
AIR TRIGGER GUNS
2 Pages
-
ULTRAMAX? PUMPING SYSTEMS
2 Pages
-
MiniLink Hydraulic System
2 Pages
-
VST-1000 LRTM Vacuum System
2 Pages
-
Flex Molding Process Seals
1 Pages
-
Pro Gun - Gelcoat
2 Pages
-
ProRider Gelcoat System
2 Pages
-
MiniPro Gelcoat System
2 Pages
-
APS Gelcoat System
2 Pages
-
Patriot Gelcoat Systems
2 Pages
-
Talon Gun - Chop/Wetout
2 Pages
-
Internal Mix Pro Gun
2 Pages
-
MiniPro Chop/Wetout System
2 Pages
-
UltraMAX Chop/Wetout System
2 Pages
-
Patriot Chop/Wetout System
2 Pages
-
APS System
2 Pages
-
Foam polyurea brochure
2 Pages
-
Megaject MkV System - ML1416
2 Pages
-
UltraMAX Gel Brochure-ML1428
2 Pages
-
APS Gel Brochure - ML1439
2 Pages
-
Pro Gun Brochure-ML1450
2 Pages
Archived catalogs
-
Reciprocator Brochure-ML1403
2 Pages
-
Quick Shot Brochure-ML143
2 Pages
-
DP-1000 Brochure-ML1406
2 Pages
-
Venus-VersaWinder-Bro
2 Pages
-
Ultra-Winder Brochure-ML1400
2 Pages
-
Tips Catalog-ML1471
16 Pages
-
Sebico Article
2 Pages
-
PrecisionTECHCatalog-Rev1104
22 Pages
-
FIT Technology Update
2 Pages
-
FIT Technology info
7 Pages
-
Econo-Winder Brochure-ML1401
2 Pages