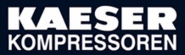
Catalog excerpts
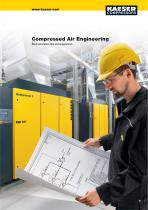
Compressed Air Engineering Basic principles, tips and suggestions
Open the catalog to page 1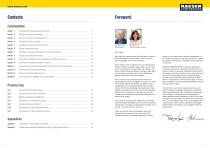
Dipl.-Wirtsch.-Ing. Thomas Kaeser Dipl.-Wirtsch.-Ing. Tina-Maria Vlantoussi-Kaeser Dear reader, More than two thousand years ago, Socrates, the famous Greek philosopher, succinctly said: “There is only one good, knowledge, and one evil, ignorance.” These ancient words of wisdom from one of the founding fathers of Western civilisation apply today more than ever, since nothing seems more permanent than change. The ever-increasing scope and speed of change brought about by technological evolution and economic globalisation demand new answers and new strategies. Now, more than ever, challenges...
Open the catalog to page 2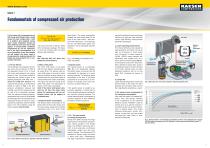
Fundamentals of compressed air production 1. Free air delivery The air delivery of a compressor (known also as the free air delivery or FAD) is the expanded volume of air it forces into the air main (network) over a given period of time. The correct method of measuring this volume is given in the following standards: DIN 1945, Part 1, Annex F and ISO 1217, Annex C. The measurement process is performed as follows as shown in Fig. 1: the temperature, atmospheric pressure and humidity must first be measured at the air inlet of the compressor package. Then, the maximum working pressure,...
Open the catalog to page 3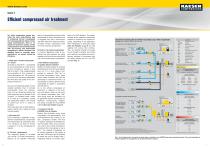
Efficient compressed air treatment So, which compressor system provides the most cost-effective way of producing oil-free compressed air? Leaving aside the claims of individual manufacturers, there is no doubt that premium quality, oil-free compressed air can be achieved both with dry-running and fluid-cooled compressors. Ideally therefore, the deciding factor to consider when selecting an air system should be efficiency. 1. What does “oil-free compressed air” mean? According to ISO 8573-1, compressed air can be described as oil-free if its oil content (including oil vapour) is less than 0.01...
Open the catalog to page 4
1. A practical example If a fluid- / oil-cooled rotary screw compressor draws in 10 m³ of air per minute at 20 °C at atmospheric pressure and with a relative humidity of 60 %, this air will contain approximately 100 g of water vapour. If this air is compressed to an absolute pressure of 10 bar at a compression ratio of 1:10, then this is referred to as 1 working cubic metre. However, at a temperature of 80 °C after compression, the air is capable of absorbing up to 290 g of water per cubic metre. As only approx. 100 g is available, the air is very dry with a relative humidity of...
Open the catalog to page 5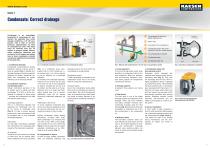
Condensate: Correct drainage Condensate is an unavoidable by-product of compressed air production. We explained how, under average conditions, a 30 kW compressor with a FAD of 5 m³/min produces approximately 20 litres of condensate per shift. This liquid must be removed from the air system to prevent system failures, costly production downtime and corrosion. In this chapter we explain how to drain condensate correctly and achieve significant cost-savings at the same time. 1. Condensate drainage Condensate, contaminated by diverse pollutants, collects at certain points in every air system...
Open the catalog to page 6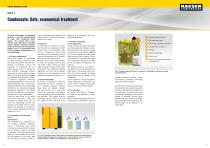
Condensate: Safe, economical treatment The term ‘condensate’ is misleading because it could be misunderstood to mean only condensed water vapour. Be careful! Every compressor works just like an oversized vacuum cleaner: it draws in contaminated air from the surroundings and passes it on in a concentrated form in the untreated compressed air to the condensate. 1. Why treat condensate? Users who dispose of condensate by simply pouring it down the drain risk heavy fines. Why? Because condensate accumulating during the production of compressed air is a highly noxious mixture. In addition to...
Open the catalog to page 7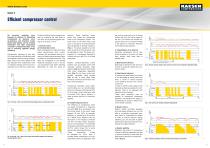
Efficient compressor control 100 Full load t2 Idle Stop Time Fig. 1: Full load – Start / stop control with fixed idling periods, so-called Dual control Pmax Pmin Idle Stop Time Fig. 2: Full load – Idle – Start / stop control with automatic optimal mode selection, so-called Quadro control Proportional controllers using intakeside throttling are not recommended, since the compressor still requires 90 % of the energy it would otherwise need to provide 100 % free air delivery, in order to deliver just 50 % of maximum capacity. b) Variable frequency drive The efficiency of compressors which are...
Open the catalog to page 8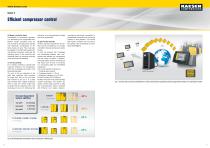
Efficient compressor control b) Master controller tasks Coordination of compressor operation is a demanding and complicated task. Modern master controllers must not only be able to simultaneously activate and deactivate compressors of differing make and size. They must also be capable of monitoring the system for maintenance purposes, balancing the operating hours of the machines and recording alarms to minimise servicing costs and maximise reliability. c) Correct grading For a master controller to operate with maximum efficiency, the compressors within the compressed air station must be...
Open the catalog to page 9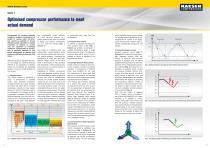
Optimised compressor performance to meet actual demand Within the scope of regulation and control technology, the systems generally referred to as compressor controllers should be considered as regulating systems. These are chiefly divided into four groups: 1. Cascade control The classic method of controlling a group of compressors is cascade control. Each individual compressor is assigned lower and upper pressure set points that either add or subtract compressor capacity to meet system demand. If several compressors are to be coordinated, this strategy results in a cascaded, or stepped...
Open the catalog to page 10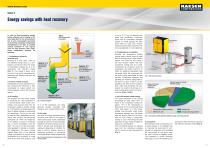
Energy savings with heat recovery In view of ever-increasing energy prices, efficient use of energy is not only important for the environment, but is also increasingly becoming an economic necessity. Compressor manufacturers are able to provide various solutions in this regard, such as heat recovery with rotary screw compressor systems for example. 1. Compressors primarily generate heat Amazing as it may seem, 100 % of the electrical energy input to a compressor is turned into heat. The action of compression charges the air in the compressor with potential energy (Fig. 1). This energy is...
Open the catalog to page 11All KAESER KOMPRESSOREN catalogs and brochures
-
Compressed Air Treatment
4 Pages
-
Marine compressors
23 Pages
-
Series KF F6 to F320
11 Pages
-
BSD series
9 Pages
-
CSD(X) Series
24 Pages
-
SX series 2.2–5.5 kW
9 Pages