
Catalog excerpts
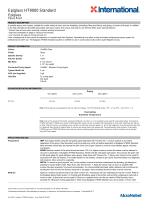
Epiglass HT9000 Standard Epiglass Epoxy Resin PRODUCT DESCRIPTION A versatile epoxy resin system, suitable for a wide variety of uses, such as sheathing, laminating, filling and fairing, and gluing, on boats of all types. In addition to the high strength and durability associated with epoxy resins, this unique and easytouse formula offers many special features: * Solvent free and low odour ensuring a cleaner working environment. * Improved workability to adapt to varying environments * Low viscosity for ease of mixing and wet out From a background of thirty years of experience in Australia and New Zealand, International now offers a tried and tested multipurpose epoxy system for professional and DIY use. The Epiglass HT9000 Standard system is certified for use in constructions built under Lloyd's Register survey. PRODUCT INFORMATION Colour Specific Gravity Volume Solids Converter/Curing Agent YAA904 Standard Curing Agent Typical Shelf Life Unit Size DRYING/OVERCOATING INFORMATION Drying 15°C (59°F) Note: Pot life reduces as temperature and mix volume increases. Thin Film Working Times: 15°C 4 hrs; 25°C 2 hrs; 35°C 1 hr Overcoating Substrate Temperature Note: Due to the variety of film builds, and hence different cure times, it is not possible to give specific overcoating times. Overcoating HT9000 with itself: HT9000 resin and/or HT9000 glue/filler mixes may be overcoated with themselves or each other whilst they are still wet or tacky. After this period, overcoating can be carried out whilst the mixes are green (i.e. soft to the fingernail). Once the products feel hard to a fingernail they should be washed down to remove any amine bloom and sanded well. Overcoating with other products: Overcoating HT9000 resin or HT9000 Filler/Glue mixes with any solvent containing paints should not be carried out until the surfaces can be sanded using 80120 grit paper. GRP Thoroughly abrade using 80120 grade paper.Degrease with Thinners No. 7. Ensure surface is dry before application of the epoxy. New laminates must be at least one month old before application of Epiglass HT9000 Standard. New laminates should also be cleaned first with Yacht Line Super Cleaner to remove mould release agents, silicones and grease. WOOD Moisture content of the wood should be below 12%. For higher moisture content the timber must be allowed to dry prior to application of Epiglass HT9000 Standard. Abrade with 80120 grade (grit) paper. Sand across the grain with 4060 grade paper for good adhesion when gluing. Wipe down with Thinners No. 7. Epoxy resin should not be used for structural work with oily timbers. For smaller repairs on oily timbers, abrade as per above recommendation and degrease with acetone. Allow solvent to evaporate. METAL To ensure a good physical 'key' on the surface, remove all surface contaminants by abrading, grit blasting or grinding to expose bright metal. Wipe down with Thinners No. 7. Apply the epoxy resin as soon as possible after surface has been prepared, to prevent deoxidisation. For Aluminium/Bronze/Lead, better adhesion will be achieved by sanding the resin mix into the surface using wet or dry paper. Hard anodised aluminium alloy must be removed. Apply to a surface preprimed with a thin layer of resin mix. Techniques will vary depending on the job in hand. Refer to the Epiglass Epoxy Resin Guide. For Coating and Sheathing, apply a first primer coat and then subsequent coats with a brush or roller. A glue brush can be used for Gluing or a spatula which can also be used for Fillet Bonding. Use a spreader for Filling and Fairing applications. When using Epiglass HT9000 Standard as a wood sealer, or even when sheathing wood, it is beneficial to saturate the wood with a 100% diluted resin mix. This will further improve adhesion. Diluted layers must be fully cured prior to application of subsequent (unthinned) coats. A hot air gun or alternatively a hair dryer can be used to warm the epoxy and shorten its cure time, whilst promoting good penetration of most wood Please refer to your local representative or visit www.yachtpaint.com for further information. types without the need for solvent addition. Pot life reduces as temperature and mix volume increases Ultra violet light All trademarks mentioned in this publication are owned by, or licensed to, the AkzoNobel group of companies. © AkzoNobel 2017. will break down the epoxy over time and the completed work should therefore be painted or varnished. A range of International primers, undercoats and fin
Open the catalog to page 1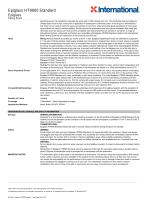
METAL To ensure a good physical 'key' on the surface, remove all surface contaminants by abrading, grit blasting or grinding to expose bright metal. Wipe down with Thinners No. 7. Apply the epoxy resin as soon as possible after surface has been prepared, to prevent deoxidisation. For Aluminium/Bronze/Lead, better adhesion will be achieved by sanding the resin mix into the surface using wet or dry paper. Hard anodised aluminium alloy must be removed. Epiglass HT9000 Standard Apply to a surface preprimed with a thin layer of resin mix. Techniques will vary depending on the job in hand. Refer...
Open the catalog to page 2All International Yacht Paint catalogs and brochures
-
Interprotect
2 Pages
-
Liquid Rubbing
2 Pages
-
Cruiser 200
2 Pages
-
Boatguard 100
2 Pages
-
Interstrip AF
1 Pages
-
Gelshield 200
2 Pages
-
Watertite
2 Pages
-
Super Cleaner
2 Pages
-
Original
2 Pages
-
Trilux 33
2 Pages
-
Trilux Prop-O-Drev
2 Pages
-
VC 17m Extra
2 Pages
-
Perfection Undercoat
2 Pages
-
Interdeck
2 Pages
-
Danboline
2 Pages
-
Yacht Primer
2 Pages
-
Woodskin
2 Pages
-
VC Offshore EU
2 Pages
-
Perfection Plus
2 Pages
-
Goldspar Satin
2 Pages
-
Compass
2 Pages
-
Schooner
2 Pages
-
Pre-Kote
2 Pages
-
Thinner No. 9
1 Pages
-
Thinner No.7
1 Pages
-
Matting Additive
2 Pages
-
VC Tar2
2 Pages
-
Primocon
2 Pages
-
Perfection
2 Pages
-
Interprime 820
2 Pages
-
Interfill 833
2 Pages
-
Interfill 830
2 Pages
-
Super Gloss HS
2 Pages
-
Cruiser Uno EU
2 Pages
-
Toplac
2 Pages
-
Micron Extra
2 Pages
-
Micron 66
2 Pages
-
Interspeed Ultra
2 Pages
-
Interprime 450
2 Pages
-
Gelshield Plus
2 Pages
Archived catalogs
-
Fibreglass Surface Prep
2 Pages