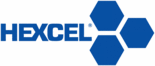
Catalog excerpts
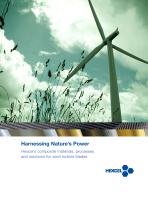
Harnessing Nature’s Power Hexcel’s composite materials, processes and solutions for wind turbine blades
Open the catalog to page 1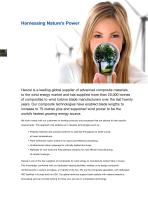
Harnessing Nature’s Power Hexcel is a leading global supplier of advanced composite materials to the wind energy market and has supplied more than 20,000 tonnes of composites to wind turbine blade manufacturers over the last twenty years. Our composite technologies have enabled blade lengths to increase to 75 metres plus and supported wind power to be the world’s fastest growing energy source. We work closely with our customers to develop products and processes that are tailored to their specific requirements. This approach has enabled us to develop technologies such as: • repreg materials...
Open the catalog to page 2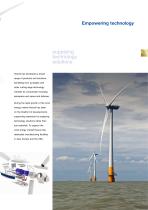
Empowering technology supplying technology solutions Hexcel has developed a broad range of products and solutions benefiting from synergies with other cutting edge technology markets for composites including aerospace and space and defense. During the rapid growth of the wind energy market Hexcel has been on the forefront of developments supporting expansion by supplying technology solutions rather than just materials. To support the wind energy market Hexcel has dedicated manufacturing facilities in Asia, Europe and the USA. captions?
Open the catalog to page 3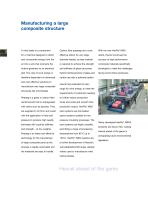
Manufacturing a large composite structure A wind blade is a component Carbon fibre prepregs are a cost for a machine designed to direct effective option for very large resins, Hexcel continues the and concentrate energy from the diameter blades, as less material success of high performance air into a wire that connects the is required to achieve the strength composite materials specifically turbine generator to an electrical and stiffness of glass structures. developed to meet the challenges grid. The cost of such energy is Hybrid reinforcements of glass and facing wind turbine producers....
Open the catalog to page 4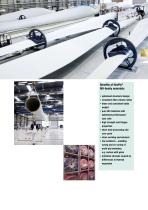
Benefits of HexPly® M9-family materials: • optimised structural design • consistent fibre volume ratios • ower and consistent blade l weight • ure UD materials with p optimised performance/ cost ratio • igh strength and fatigue h properties • hort total processing and s cure cycle • clean working environment • ow exotherm – enabling l curing and co-curing of multi-ply laminates, e.g. carbon with glass • inimise stresses caused by m differences in thermal expansion
Open the catalog to page 5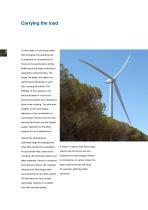
A wind blade is a structural beam that throughout its operating life is subjected to considerable lift forces on its aerodynamic profile. Stiffening of the blade is therefore essential to resist bending. The longer the blade, the higher the performance demands on such load carrying structures. The stiffness of the material in the structural beam is crucial as it prevents the blade from striking the tower when rotating. The structural integrity of the wind blades depends on the combination of composites used to build the load carrying structures and the highest quality materials are...
Open the catalog to page 6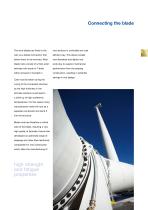
The wind blades are fixed to the root sections in controlled and cost hub via a bolted connection that efficient way. This allows smaller allows them to be removed. Most root diametres and lighter root blade roots consist of a thick solid ends due to superior mechanical laminate with studs or T-bolts performance from the prepreg either screwed or bonded in. construction, resulting in potential Care must be taken during the curing of the composite structure as the high thickness in the laminate sections could lead to a build-up of high exothermic temperatures. For this reason many...
Open the catalog to page 7
Optimising thick structures Polyspeed® pre-cured glass/ where reactive liquid systems carbon/epoxy laminates are used need to be combined with solid, in conjunction with prepreg in a already cured, composite parts. vacuum bag lay-up to improve the They enable large structures to quality and optimise the structure of cured stacks. Polyspeed® by combining infusion technology pre-cured laminates are available with laminates or other pre-cured load carrying structures such as constructions fully supporting pultruded components. the mechanical performance of vacuum bag cured structures. As the...
Open the catalog to page 8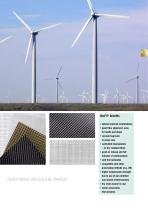
HexFIT® Benefits • optimal material combinations • good fibre alignment, easy to handle and drape • vacuum bag/oven or press cure • controlled impregnation – no dry residual fibres • good air release and full infusion of reinforcement • void free laminates • compatible with other processing methods (e.g. LRI) • higher compression strength optimised structural design due to use of non-stitched non-woven reinforcements • dry resin cleaner to use • easier processing than prepreg
Open the catalog to page 9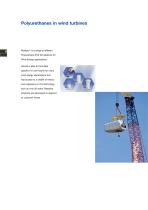
Polyurethanes in wind turbines Modipur® is a range of different Polyurethane (PU) formulations for Wind Energy applications. Hexcel is able to formulate specific PU core foams for many wind energy applications and has access to a wealth of history and experience in PU technology built up over 30 years. Bespoke products are developed to respond to customer needs. PICTURE (Nacelles); rely on Franz
Open the catalog to page 10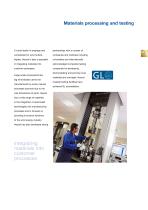
Materials processing and testing A world leader in prepregs and partnerships with a number of composites for wind turbine companies and institutes including blades, Hexcel is also a specialist in integrating materials into acknowledged composite testing customer processes. Large scale components like big wind blades cannot be manufactured by purely manual processes anymore due to the vast dimensions of parts. Hexcel has a wide range of expertise in the integration of automated technologies into manufacturing processes and is focused on providing innovative solutions to the wind energy...
Open the catalog to page 11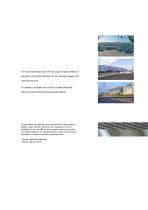
For more information and the full range of data sheets for Hexcel’s composite materials for wind energy please visit www.hexcel.com To contact us please find our list of sales offices at: www.hexcel.com/OurCompany/sales-offices All information is believed to be accurate but is given without liability. Users should make their own assessment of the suitability of any product for the purposes required. All sales are made subject to our standard terms of sale which include limitations on liability and other important items. Hexcel registered trademark Hexcel February 2012
Open the catalog to page 12All Hexcel Composites catalogs and brochures
-
Rail
5 Pages
-
Wind_Turbine_Blades
12 Pages
-
Automotive Product Focus
4 Pages
-
Winter_Sports_Brochure
6 Pages
Archived catalogs
-
HexTow® Chopped Fiber
2 Pages
-
HexMC®-i / C / 2000 / M81
2 Pages
-
HexMC®-i / C / 2000 / M77
2 Pages
-
Redux ® 100 series
4 Pages
-
HexPly ® M78.1
4 Pages
-
A1 & A10
4 Pages
-
HexMC
6 Pages
-
MARKET BROCHURES-Rail
5 Pages
-
HexPly® M81
4 Pages
-
HexPly® M77
3 Pages
-
HexPly® M10R
4 Pages
-
HexPly® M47
4 Pages
-
HexPly® M49
4 Pages
-
HexForce_Technical_Fabrics_Handbook
116 Pages
-
HexWeb_Acousti-Cap
4 Pages
-
HexPly M9M10
4 Pages
-
CarbonFiber_SelectorGuide_us
4 Pages
-
HexPly® M34
4 Pages
-
HexForce? Fiber Glass Fabric
1 Pages
-
HexForce? Aramid Fabric
1 Pages
-
Redux epoxy film adhesive
4 Pages
-
Honeycomb
40 Pages