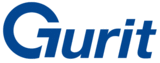
Catalog excerpts
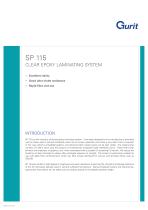
SP 115 CLEAR EPOXY LAMINATING SYSTEM ¬ Excellent clarity ¬ Good ultra-violet resistance ¬ Rapid fibre wet-out INTRODUCTION SP 115 is a low viscosity, ultra-clear epoxy laminating system. It has been designed for the manufacture of laminates such as those used in sail and surfboards which are to remain unpainted, and where a very clear finish is required. In this way colourful embedded graphics and attractive fabric weave styles can be kept visible. The material also contains UV filters which give the product its characteristic transparent pale violet/blue colour. These filters both enhance the sharpness of graphics, and, when overcoated with a suitable UV-screening PU varnish, will reduce the tendency of clear laminates to yellow after prolonged exposure to sunlight. The product is particularly suitable for use with glass fibre reinforcements which use fibre sizings optimised for wet-out and laminate clarity, such as RE210D. SP 115 also exhibits a high degree of toughness and water resistance, enhancing the strength and damage tolerance of the thin laminates typically used in sail and surfboard manufacture. Being completely solvent and styrene-free, polystyrene foam blanks can be safely used to produce boards of the lightest possible weight.
Open the catalog to page 1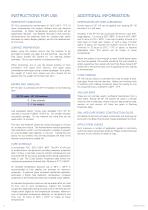
INSTRUCTIONS FOR USE WORKSHOP CONDITIONS SP 115 is optimised for use between 18 - 25°C / 64°F - 77°F At lower temperatures the product thickens and may become unworkable. At higher temperatures working times will be significantly reduced. Low Relative Humidity (<70%) and dry reinforcements are essential, both for creating high clarity laminates to clearly display graphics, and for the development of a full cure. SURFACE PREPARATION Before using the product ensure that the surfaces to be laminated or coated are clean, dry and dust-free. Use only SP Fast Epoxy Solvent (SP Solvent A) for...
Open the catalog to page 2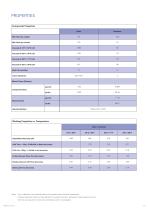
Notes: For an explanation of test methods used see 'Formulated Products Technical Characteristics'. All figures quoted are indicative of the properties of the product concerned. Some batch to batch variation may occur. tAll times are measured from when resin and hardener are first mixed together.
Open the catalog to page 3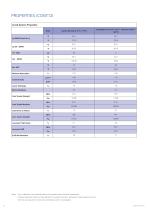
Notes: For an explanation of test methods used see 'Formulated Products Technical Characteristics'. All figures quoted are indicative of the properties of the product concerned. Some batch to batch variation may occur. tAll times are measured from when resin and hardener are first mixed together.
Open the catalog to page 4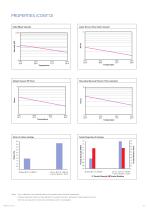
PROPERTIES (CONT’D) Initial Mixed Viscosity Latest Time for Flow Under Vacuum† Earliest Vacuum Off Time† Theoretical Demould Time for Thin Laminates† Strain to Failure Castings Tensile Properties of Castings 76 28 days @ 21°C / 69.8°F Tensile Strength For an explanation of test methods used see ‘Formulated Products Technical Characteristics’. All figures quoted are indicative of the properties of the product concerned. Some batch to batch variation may occur. †All times are measured from when resin and hardener are first mixed together.
Open the catalog to page 5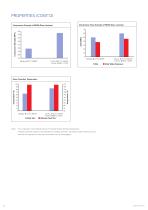
Compressive Strength of RE300 Glass Laminate Interlaminar Shear Strength of RE300 Glass Laminate 450 ■ Dry ■ After Water Exposure Glass Transition Temperature 28 days @ 21°C/69.8oF Peak TanS 69.8oF +16 hrs. @ 50°C /122°F ] Ultimate Peak TanS Notes: For an explanation of test methods used see 'Formulated Products Technical Characteristics'. All figures quoted are indicative of the properties of the product concerned. Some batch to batch variation may occur. tAll times are measured from when resin and hardener are first mixed together.
Open the catalog to page 6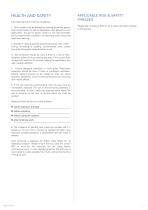
The following points must be considered: 1. Skin contact must be avoided by wearing protective gloves. Gurit recommends the use of disposable nitrile gloves for most applications. The use of barrier creams is not recommended, but to preserve skin condition a moisturising cream should be used after washing. 2. Overalls or other protective clothing should be worn when mixing, laminating or sanding. Contaminated work clothes should be thoroughly cleaned before re-use. 3. Eye protection should be worn if there is a risk of resin, hardener, solvent or dust entering the eyes. If this occurs...
Open the catalog to page 7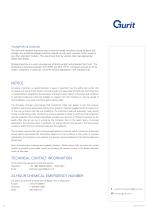
TRANSPORT & STORAGE The resin and hardener should be kept in securely closed containers during transport and storage. Any accidental spillage should be soaked up with sand, sawdust, cotton waste or any other absorbent material. The area should then be washed clean (see appropriate Safety Data Sheet). Storage should be in a warm dry place out of direct sunlight and protected from frost. The temperature should be between 10°C (50°F) and 25°C (77°F). Containers should be firmly closed. Hardeners, in particular, will suffer serious degradation if left exposed to air. NOTICE All advice,...
Open the catalog to page 8All Gurit catalogs and brochures
-
GURIT® BALSAFLEX™
4 Pages
-
CORECELL™ S
3 Pages
-
CORECELL™ T
3 Pages
-
GURIT® PVC
3 Pages
-
CORECELL™ A
3 Pages
-
SPABOND™ 345
7 Pages
-
SPABOND™ 730
4 Pages
-
Formulated Products Brochure
23 Pages
-
T-Prime 160
8 Pages
-
T-Prime 130-1 (v5)
8 Pages
-
SMARTCURE™ (v9)
4 Pages
-
System SPRINT™ Resin (v2)
4 Pages
-
T-Lam 130-1 Slow
6 Pages
-
T-Gel 130-1
6 Pages
-
T-Paste 70-2
6 Pages
-
CR 3400
5 Pages
-
Gurit® Kerdyn® Green
4 Pages
-
Marine Market Summary (v1)
2 Pages
-
Hetairos_Gurit_Project
2 Pages
-
Aerospace
2 Pages
-
PB1000
4 Pages
-
HI-PANEL
2 Pages
-
Gurit G-PET
1 Pages
-
GURIT PRODUCT CATALOGUE 2016
88 Pages
-
Eposeal 300
6 Pages
-
Ampreg 26
8 Pages
-
Ampreg 21FR
6 Pages
-
ST 95
6 Pages
-
PREPREGS
11 Pages
-
Hi-Panel Product Brochure
2 Pages
-
CORE MATERIALS
9 Pages
-
ADHESIVES
5 Pages
-
WE91 - 2
4 Pages
-
WE91 - 1
4 Pages
-
SE 85 GT
5 Pages
-
SE 85
5 Pages
-
SE 84 Nano
5 Pages
-
PH 840
4 Pages
-
PN 901
4 Pages
-
SE 300
4 Pages
-
SC 110
4 Pages
-
SE 200
5 Pages
-
ST 16
4 Pages
-
SE 84LV
6 Pages
-
ST 70
6 Pages
-
SE 70
5 Pages
-
SPABOND 340LV HT
6 Pages
-
SPABOND 345
4 Pages
-
SPABOND 340
7 Pages
-
SPABOND 340LV
6 Pages