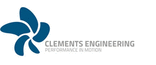
Catalog excerpts
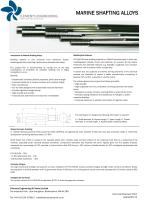
MARINE SHAFTING ALLOYS Introduction to Marine Shafting Alloys Metallurgical features Shafting material is now produced from advanced ‘duplex’ metallurgically structured high performance stainless steel alloys. F51 DUPLEX boat shafting material is a DUPLEX stainless steel in which two crystallographic phases, ferrite and austenite, are present. By this means enhanced and desirable features e.g. Strength, toughness and corrosion resistance, can be present within a single alloy. F51 Duplex—This is recommended as having one of the best combinations of properties for propeller shafting and is highly competitive in price. Benefits: • Substantially increased physical properties, particularly strength • Improved resistance to crevice corrosion and corrosion fatigue • More cost effective • Can be safely designed with substantially reduced diameters • Provides significant weight saving • High strength and ductility • Improved boat performance and economy of installation To attain this, the austenite and ferrite forming elements of the chemical analysis are controlled to ensure a stable microstructure comprising of between 35% to 50% austenite in a ferritic matrix. The metallurgical structure gives the following benefits: • High strength • High toughness from the combination of strong austenite with ductile ferrite • Resistance to stress corrosion cracking (SCC) is raised by the ferrite • Corrosion pitting resistance and ductility due to Nitrogen, a potent austenite stabiliser • Improved resistance to abrasion and erosion at high flow rates. For submission for designs the following information is required: A – Shaft diameter, B- Keyway length, C- Taper Length, D- Thread Diameter, E- Thread length, F- Keyway depth, G-Keyway Width. Stress Corrosion Cracking In chloride bearing solutions ferritic-austenitic steels (DUPLEX) are significantly more resistant to SCC than low alloy austenitic (316) or martensitic precipitation hardening stainless steels (17 4PH) Shaft failure due to SCC is caused in the stainless steels when complex oxide corrosion product at the molecular level lead to a weakening of the material, especially under cyclically stressed conditions. Comparative laboratory test illustrate this point. Figures given are the applied stresses, expressed as a percentage of UTS, required to induce failure after 500 hours in 40% calcium chloride solution at 100◦ centigrade (accelerated test conditions) F51 DUPLEX – 90% 17 4PH (Martensitic PH) – 10% 316 Stainless (Austenitic) – 30% Corrosion Fatigue The high mechanical strength and superior corrosion resistance of F51 DUPLEX ensures excellent fatigue strength under corrosive conditions. Rotary bending tests in artificial seawater at 40 C gives stress levels of 430 N/sq. mm to bring about rupture of smooth samples after 20 million cycles at 600 RPM. Intergranular Corrosion The carbon content of F51 DUPLEX is kept below 0.03% to avoid intergranular corrosion. Clements Engineering (St Neots) Limited The Industrial Park, Little Staughton, Bedfordshire, MK44 2BN Tel: +44 (0)1234 378814 sales@clementsmarine.co.uk
Open the catalog to page 1All Clements Engineering Ltd catalogs and brochures
-
Propeller
2 Pages
-
MARINE BEARINGS
2 Pages
-
Shaft Seals
2 Pages
-
PROPELLER SPECIFICATIONS
2 Pages
Archived catalogs
-
Marine bearing
2 Pages
-
Rudder bearing system
2 Pages
-
Rudder tubes
2 Pages
-
Marine Corrosion
2 Pages
-
Marine Shafting Alloys
2 Pages