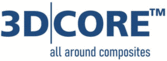
Catalog excerpts
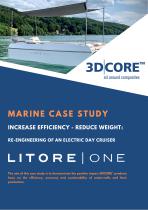
MARINE CASE STUDY INCREASE EFFICIENCY - REDUCE WEIGHT: RE-ENGINEERING OF AN ELECTRIC DAY CRUISER
Open the catalog to page 1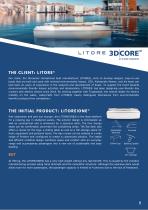
THE CLIENT: LITORE® Our client, the Slovenian recreational boat manufacturer LITORE®, aims to develop elegant, easy-to-use boats that are built and used with minimal environmental impact. CEO, Aleksander Nemec, and his team can look back on years of experience in the research and development of boats. To support the trend towards environmentally friendly leisure activities and deceleration, LITORE® has been designing user-friendly day cruisers with electric motors since 2018. By working together with Torqeedo®, the market leader for electric mobility on the water, watercrafts from LITORE®...
Open the catalog to page 2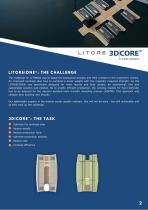
LITORE|ONE®: THE CHALLENGE The challenge for LITORE® was to adapt the production process and their product to the customers' wishes. An improved laminate plan had to combine a lower weight with the originally required strength. As the LITORE|ONE® was specifically designed for hotel resorts and boat rentals, an economical, fast and sustainable solution was needed. So to enable efficient production, the existing moulds for hand laminate had to be adapted for the vacuum assisted resin transfer moulding process (VARTM). This approach was cheaper than building new moulds. Our lightweight experts...
Open the catalog to page 3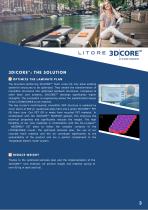
3D|CORE™: THE SOLUTION OPTIMIZE THE LAMINATE PLAN The structure-reinforcing 3D|CORE™ foam cores not only allow existing sandwich structures to be optimized. They enable the transformation of monolithic structures into optimized sandwich structures. Compared to other foam core systems, 3D|CORE™ develops significantly higher strengths. The successful re-engineering allows the sophisticated design of the LITORE|ONE® to be retained. The day cruiser's multi-layered, monolithic GRP structure is replaced by cover layers of 600 gr. quadraxial glass fibre and a green 3D|CORE™ PET GR foam core. Our...
Open the catalog to page 4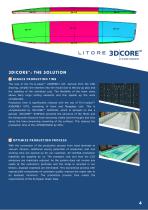
3D|CORE™: THE SOLUTION REDUCE PRODUCTION TIME The cuts of the Fix-in-place™ ASSEMBLY KIT, derived from the CAD drawing, simplify the insertion into the mould due to the lay-up plan and the labelling of the individual cuts. The flexibility of the foam cores allows fairly large cutting elements and this speeds up the work considerably. Production time is significantly reduced with the use of Fix-in-place™ ASSEMBLY KITS, consisting of foam and fibreglass cuts. This is complemented by 3D|CORE™ SURFACE, which is sprayed on like a gelcoat. 3D|CORE™ SURFACE prevents the structure of the fibres and...
Open the catalog to page 5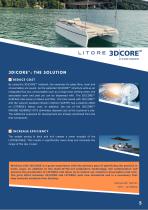
3D|CORE™: THE SOLUTION REDUCE COST By using the 3D|CORE™ material, the expenses for glass fibre, resin and consumables are saved. As the patented 3D|CORE™ structure acts as an integrated flow aid, consumables such as a large-area venting mesh, the associated resin and peel ply can be dispensed with. The 3D|CORE™ SURFACE also saves on fleece and filler. The time saved with 3D|CORE™ and the vacuum assisted infusion method (VARTM) has a positive effect on LITORE®'s labour cost. In addition, the use of the 3D|CORE™ MARINE ASSEMBLY KITS eliminates disposal cost at the customer's site. The...
Open the catalog to page 6
3D|CORE™: THE RESULT INITIAL SITUATION PASSENGER CAPACITY PRODUCTION TIME 30% weight saving in deck and hull from 290 kg to 200 kg 1/3 less material usage 100% process reliability from hand laminate to vacuum infusion 50% time saving in production 90kg higher payload from 4 (+1) to 5 (+1) passengers Longer battery life
Open the catalog to page 7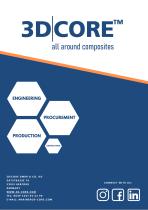
PRODUCTION CERTIFICATION
Open the catalog to page 8All 3D|CORE GmbH & Co. KG catalogs and brochures
-
3D|CORE™ Services
9 Pages
-
3D|CORE™ Markets
11 Pages
-
3D|CORE™ Technology
9 Pages
-
Fix-in-place™ ASSEMBLY KITS
5 Pages
-
3D|CORE™ PRODUCTS
6 Pages
-
TDS 3D|CORE™ PET GR
2 Pages
-
TDS 3D|CORE™ PET FR
2 Pages
-
TDS 3D|CORE™ PET
2 Pages
-
TDS 3D|CORE™ XPS
2 Pages